Danfoss Refrigeration and Air Conditioning offers a very wide range of refrigeration controllers. The Controllers are a constant source of surprise in terms of new features and parameters, but are very similar as far as their basic functions are concerned.
Danfoss Refrigeration and Air Conditioning offers a very wide range of refrigeration controllers. The Controllers are a constant source of surprise in terms of new features and parameters, but are very similar as far as their basic functions are concerned.
Below, you will find more information about refrigeration controllers and their control and monitoring functionality.
Temperature control function
In the standard version, a refrigeration controller is always equipped with a control sensor.
When used in a normal cold store, this sensor measures the room temperature. For this reason it is normally located in such a way that it records the temperature of the return airflow to the evaporator.
The refrigeration controller then displays and processes the temperature as the actual room temperature. This actual value is constantly compared with the refrigeration controller's set-point value.
The controller setpoint can accept any desired value. A hysteresis can also be set in addition to the desired value. The sum of set point plus hysteresis yields the upper activation value whereas the set point value itself represents the lower temperature control activation value.
Upon achieving the upper activation value, refrigeration (compressor) is switched on and switched off again when the desired temperature is achieved. In this way, room temperature is always kept within this range.
This temperature control function can be seen as the most important basic function of a refrigeration controller. In most cases, it is also possible to limit the range within which the operator can change the desired value. For example, the commissioning engineer can restrict the adjustment range available to operating personnel so that no damage can be caused to the refrigerated goods (and that it is not possible to set a room temperature too low or too high).
If the refrigeration controller is used not for a cold room, but for a refrigerated cabinet, it is recommended to use two sensors for controlling temperature.
The main reason for this is day/night time control. In the case of refrigerated open shelf cabinets, daytime operation differs incidental heat load during daytime or opening hours as a result of human usage.
A particular weighting of the control sensors relative to one another is usually possible and can be useful.
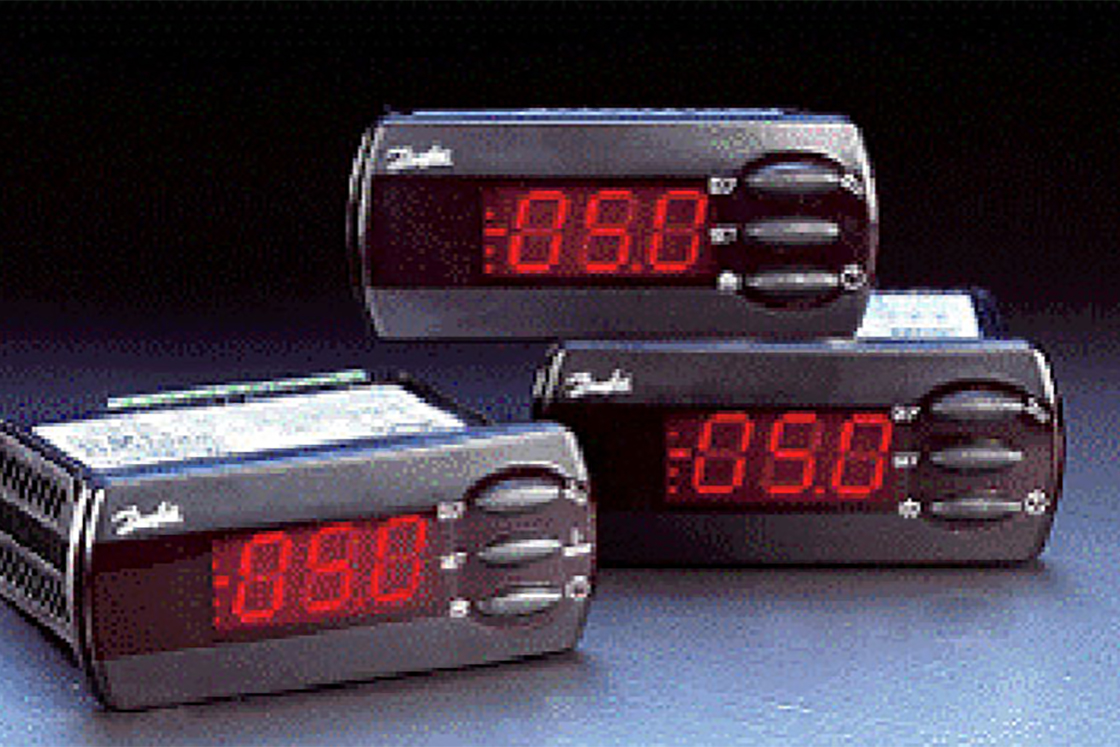
The second primary function in addition to temperature control is defrost management. The first question that arises is when defrost is to be initiated.
Start of defrost with external pulse signal
As a rule this occurs at a fixed time interval or at particular times. "Intervals" are the simplest variant. If, for example, an 8 hour time interval is entered, this means that defrost will be initiated every 8 hours.
If the controller features a real-time clock (this can be retrofitted if so required), the desired defrost times can be entered as specific times (e.g. 0900 or 1700).
A real-time clock is particularly advisable if there are specific times at which new goods are consigned to the cold room to be controlled. This avoids defrosting being initiated just when the consignment is in progress or immediately thereafter as the increased heat input as a result of new goods or opening of the door requires a refrigeration-ready refrigeration system for increased heat evacuation from the room.
A further option for initiating defrosts is manually setting it on the controller itself. This is particularly helpful for the refrigeration fitter when he is on a service call as he can simulate defrosting immediately without altering the defrost time or having to wait hours. It is also possible to initiate defrosting from an external contact. This makes sense with groups of refrigeration controllers so as to coordinate defrost times.
Defrost
Once defrost has been initiated, the way in which it normally proceeds must be defined by corresponding settings in the controller. There are fundamental differences here between re-circulation defrosting, electric defrosting and hot gas defrosting. In the case of re-circulation defrosting, the cold store temperature, which is in excess of 0°C, is used for defrosting. The evaporator fan therefore has to keep running while defrost is in progress.
This is not the case with hot gas or electric defrost. In this case the fan is switched off throughout the entire defrost procedure so as not to introduce unnecessary heat into the cold store. The fundamental objective of defrost is to re-provide a heat exchanger (evaporator) that is free of ice whereby the transfer of heat from the air in the room to the refrigerant is not hampered by the accretion of ice.
Among other things, electrical and hot gas defrost differ in that the compressor is switched off in the case of electric defrosting whereas it can be operated during defrost in the case of hot gas defrosting because the hot gas used for defrosting has to be provided by the refrigeration system itself.
Electric defrost is the most widely used method. This involves electric defrost heaters being introduced into the evaporator. The defrost process involves the defrost contact being activated by the refrigeration controller.
A defrost sensor in the evaporator package terminates the defrost as soon as the evaporator package temperature has reached the temperature set on the sensor.
As a backup, a maximum defrost time can also be set in the refrigeration controller which terminates the defrosting in the event of a defect in the defrost sensor or a similar malfunction. Upon completion, defrost is followed by the dripping time.
This time expires before the refrigeration process is reinitiated. Put simply, the dripping time serves merely to evacuate the melted ice on the evaporator via the condensate drain.
Fan control
If the compressor is restarted once the dripping time has expired, it is possible to define a fan cut-in temperature once defrost is complete. That means that the evaporator fan will only start once the defrost sensor reports a fall in the temperature to the fan cut-in temperature that is set on the refrigeration controller.
This is particularly appropriate for freezer storage to prevent "water shedding" into the room by the wet, recently defrosted evaporator, which would lead, among other things, to the formation of ice and icicles in the freezer storage room.
Simple refrigeration controllers are mainly intended for operation with thermostatic expansion valves. As such, there is no control of the expansion valve from within the controller. More complex controllers on the other hand also take on electronic injection control in addition to the normal cold room functions. For example, the type AKV electronic expansion valve is fed and controlled directly by the refrigeration controller.
This point needs to be borne in mind, especially when choosing the control transformers, as a controller supplying an AKV valve draws significantly more electrical power than a controller that only has to supply itself. It also needs to be borne in mind that electronic injection control requires a pressure transducer. This is not required for simple refrigeration controllers.
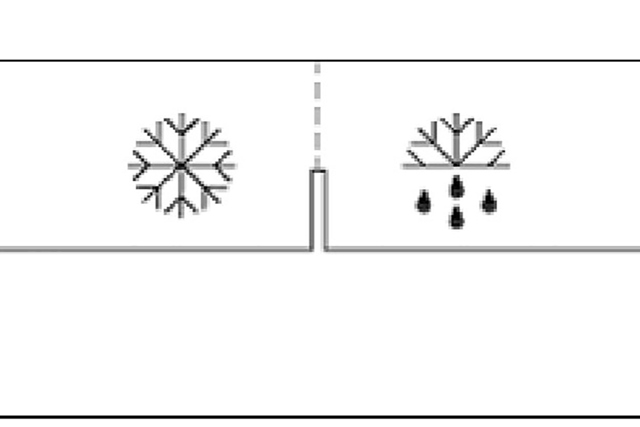
If a refrigeration controller is equipped with an electronic expansion valve it usually also has a defrost on demand function. The basic idea of defrost on demand is to ensure that no unnecessary defrost is initiated.
Defrost on demand - accumulated cooling time - defrost sensor sequence
This saves energy because even if only one defrost in five is skipped, this is already a plus.
What is important with defrost on demand is that, notwithstanding this function, defrost is only permitted at the scheduled times.
If this were not so, it might happen that defrost is commenced at an awkward time. How does the controller recognize whether or not the time is ripe for defrost? With electronic injection and with systems with one compressor, the vaporization temperature falls steadily after defrost. At the same time the degree to which the electronic expansion valve is open after defrost reduces constantly until the point where defrost is performed once again. This value is a clue for the refrigeration controller as to whether a defrost can be skipped or not.
Refrigeration controllers that do not feature electronic expansion valves have a tougher time. But they also can detect from the way the temperature is developing on the defrost sensor whether a defrost is necessary or not. Here too the temperature on the defrost sensor with 1:1 systems falls constantly - and is relative to when the last defrost occurred.
Another option is to look at total cooling time. If this is steadily increasing and it is assumed that the evaporator is thickly covered in ice then defrost should be initiated as soon as possible.
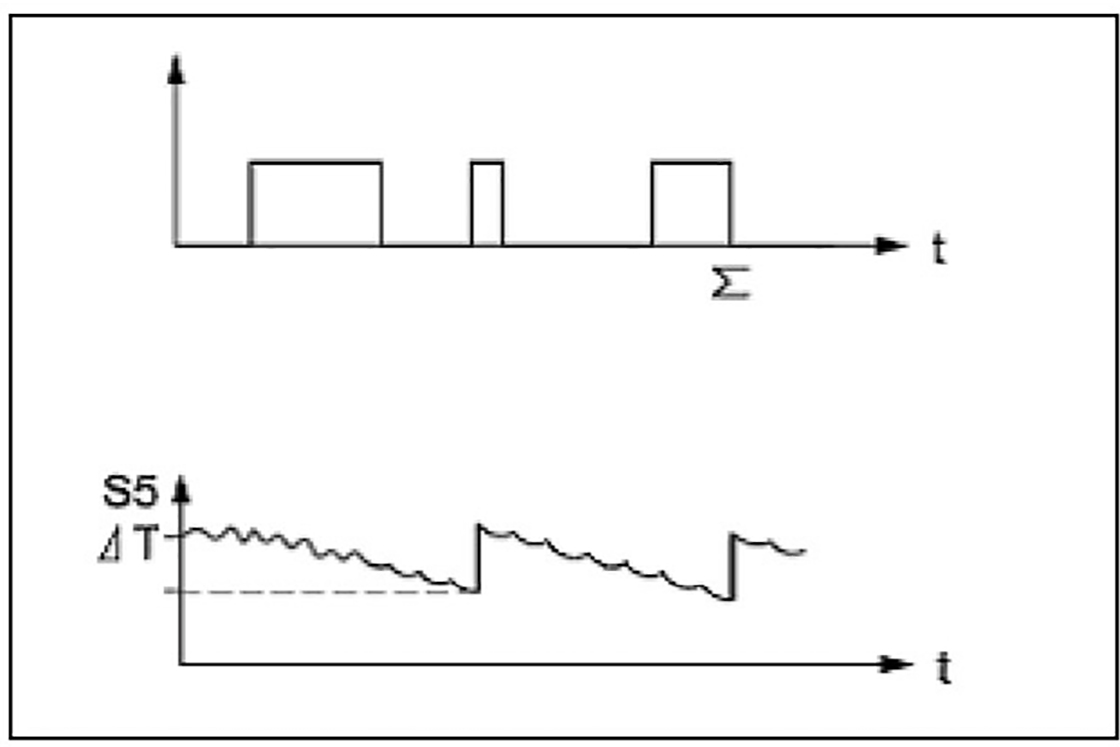
Temperature-variable resistors are commonly used as sensors in Refrigeration Controllers. Both PTC and NTC sensors are common. PTC (positive temperature coefficient) are also referred to as thermistors, namely they conduct well at low temperatures. That means that the resistance of PTC sensors increases with rising temperature.
PT1000 are common thermistor sensors with a resistance of 1000 Ohm (=1k Ohm) at 0°C. In the case of NTC sensors (negative temperature coefficient) the resistance reduces as the temperature increases. There are several temperature resistance variants (e.g. NTC 5 k Ohm, NTC 10 k Ohm) for this type of sensor.
This point is particularly important for commissioning. If the display shows a room temperature that is markedly different from the actual temperature it should be checked whether the wrong type of sensor has been used in the controller.
If the discrepancies are only very small - e.g. because of long sensor cables, which as such also constitute an electrical resistance, it is typically the case that the refrigeration controller sensor can be slightly re-calibrated.
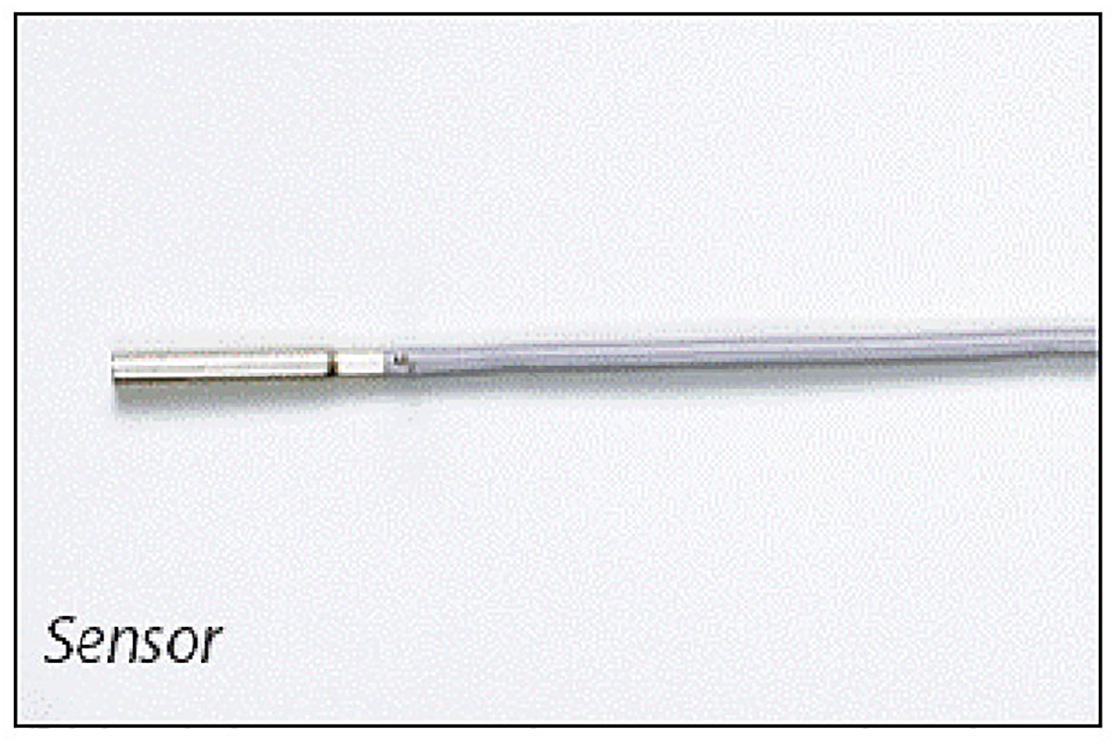
Alarm functions play an important role with refrigeration controllers.
Refrigeration controller - process with alarm
Error messages in particular, such as "Temperature too high" are readily transmitted as an alarm. To this end there is usually at least one floating alarm contact available.
This can be used to control an alarm lamp or klaxon on the control cabinet or an external dialing device for informing the janitor/or service mechanic. Nowadays of course there are numerous ways of integrating refrigeration controllers into bus and remote maintenance systems.
These systems are usually modular in construction and can be expanded at will. Other important error messages are "Sensor defect", "Temperature too low" and "Door alarm". "Sensor defect" is displayed if the resistance of the associated sensor lies outside a normal range. One option with an error message such as this is to disconnect the sensor and check the system with an ohmmeter.
If the sensor is broken (infinitely large resistance) or if the resistance is radically different from the nominal value it has to be exchanged. If it is functioning correctly then the spring-loaded connection (interface between the sensor and the controller) and other spring-loaded connectors should be checked to ensure there is good contact.
"Temperature too low" can result in damage to goods. What needs to be checked first when this fault alarm occurs is whether the refrigeration controller really does switch off the cooling output when its set point temperature is reached (lower room temperature) or whether it remains on in error.
If this is in perfect working order then the compressor contactor, for example (if there is one) needs to be inspected to establish whether it is sticking (load is switched through despite a fall in voltage). If the operator is warning that the refrigeration performance is inadequate, the door contact in particular can be very helpful. It is frequently the case that the actual number of door openings per day is much higher than the operator originally forecast and defined.
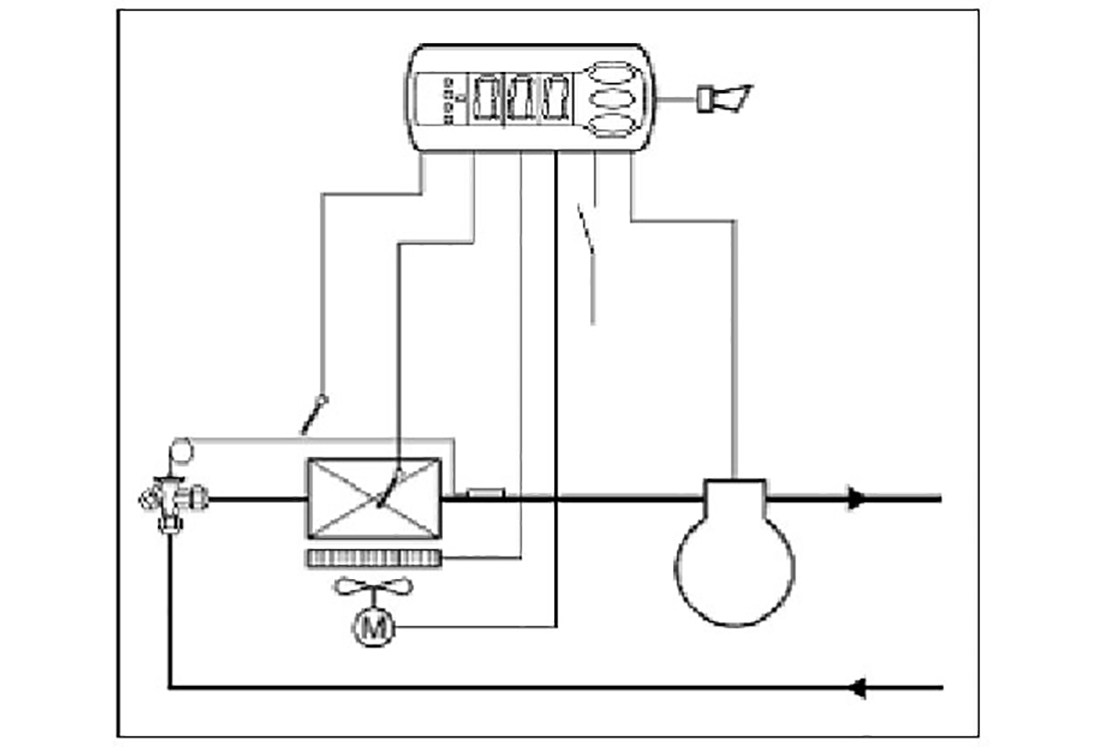
Modern controllers can also perform lighting control functions. The door contact previously referred to also lends itself to this purpose. For example, it can be used - assisted by the refrigeration controller - to switch the light on automatically as soon as someone enters the room.
Rail heating - Day/Night process
The light then automatically switches itself off again with a short two-minute time delay, for example, this being already an integral feature in many refrigeration controllers. Refrigeration controllers that are optimized for refrigerator cabinets offer the facility of controlling heating of the frame. Rail heating is important for keeping the refrigerator and freezer cabinet windows free from condensation when closed.
The primary purpose of this is to ensure that the goods on the refrigerator shelf are well presented to the supermarket customer. If the windows or window frames were not heated then condensation from the air surrounding the refrigerator cabinets would condense on the windows and one would no longer be able to see through the window panes. The rail heating function can also be used for heating freezer room door frames. Heating the door frame ensures that the doors can be opened and closed and do not freeze shut.
If there are significant discrepancies here, the remedy is to fit a simple door alarm with a short setting. If the cold store door is left open too long, the refrigeration controller will trigger an alarm. Typically this will cause operators not to leave the cold store doors open for convenience.
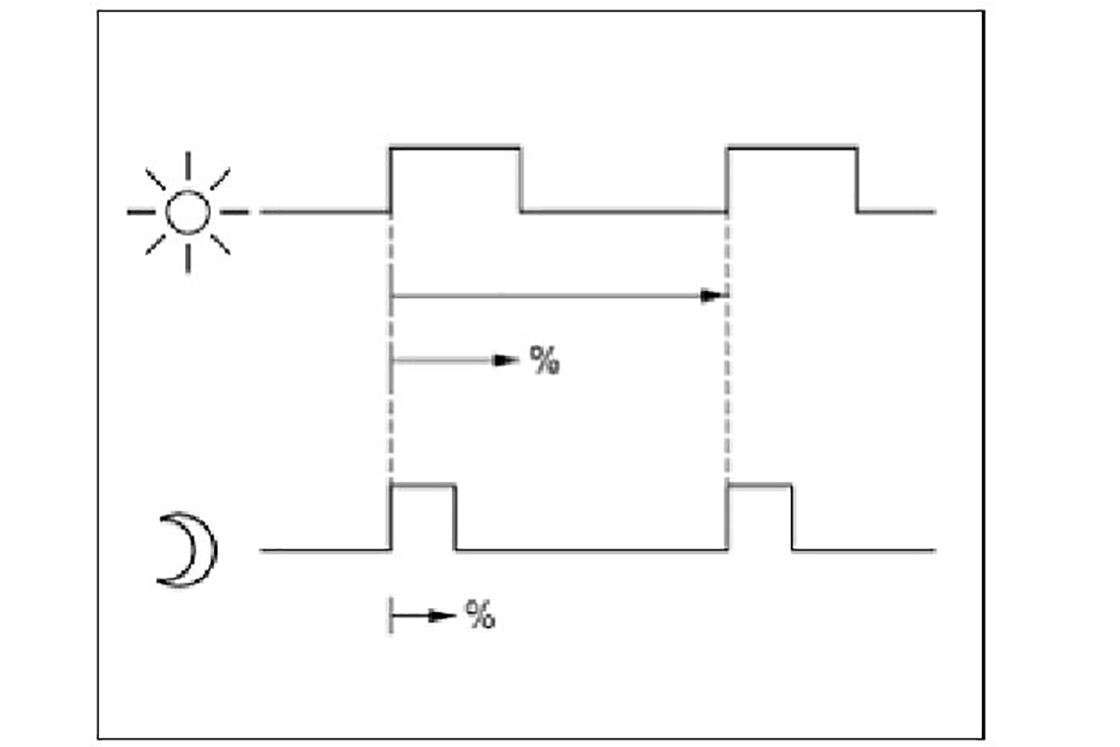
Refrigeration controllers also come fully integrated in a control box.
The benefits
The switch box is delivered ready to install, fuses, control transformer, overcurrent release for the compressor and contactors are - depending on the model - already built in and ready-wired.
An additional benefit is that the controller is perfectly integrated into the control box. This typically affords a high degree of protection and it means it can be thoroughly cleaned. It also considerably reduces fitting time, especially with three-phase systems with contactors.
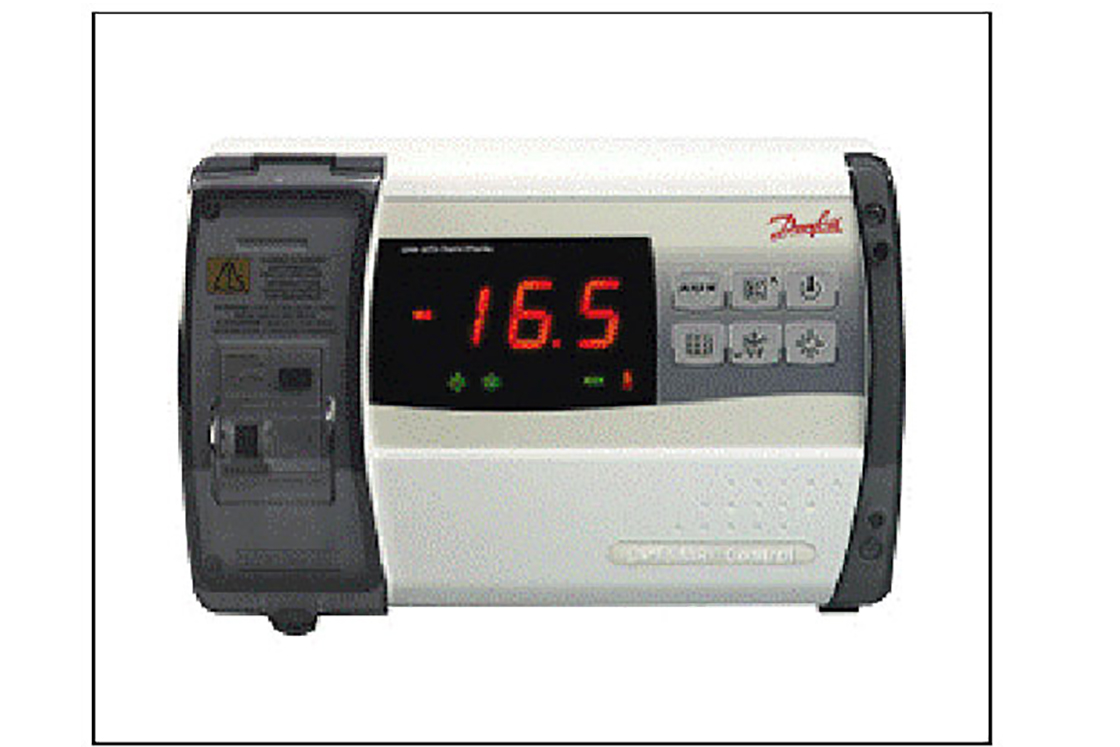