How often do you see a quantum leap in industrial design? Certainly not every day. And in the world of heat exchangers, not even every decade. In fact, the same basic heat exchanger model has been in use since the 1970s. But now, thanks to Danfoss’ latest invention – the Micro Plate Heat Exchanger – that is all about to change.
Plate heat exchangers are widely used in a number of refrigerant applications. The most commonly used technology is the chevron-type plate pattern. The manufacturing processes and the design methods are well-proven all over the world. However, conventional solutions are failing to meet the increasing demands for efficiency and sustainable development. A new technology is needed, and has been developed by Danfoss: the Micro Plate Heat Exchanger (Fig. 1).
Danfoss' MPHE technology is setting new standards in energy efficiency. Significantly improved heat transfer, reduced use of raw materials and minimal hold-up volumes bring clear economic and environmental savings. Furthermore, the unique dimple plate pattern makes the MPHE more robust. In a direct comparison with a traditional brazed plate heat exchanger (BPHE) the differences are stunning.
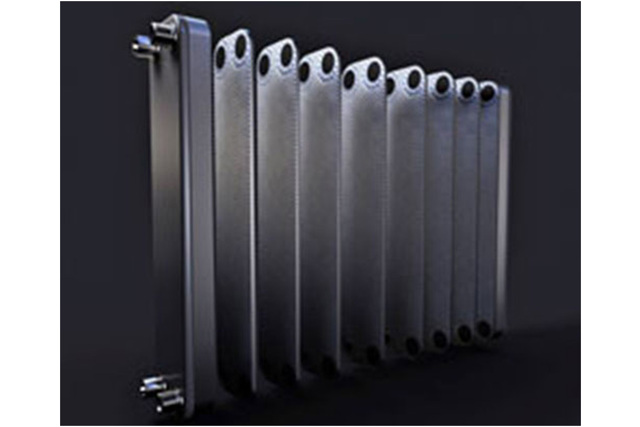
Danfoss' innovative dimple technology is the main driver for the MPHE’s higher efficiency, offering far better heat transfer because the flow around the brazing points is more uniform. Laboratory tests show that the difference between the maximum and minimum velocities in an MPHE is only 1/3 of the ratio in a traditional BPHE (Fig. 2).
The MPHE achieves an optimal balance between increased turbulence and frictional losses, significantly increasing the heat transfer coefficient and improving efficiency (Fig. 3).
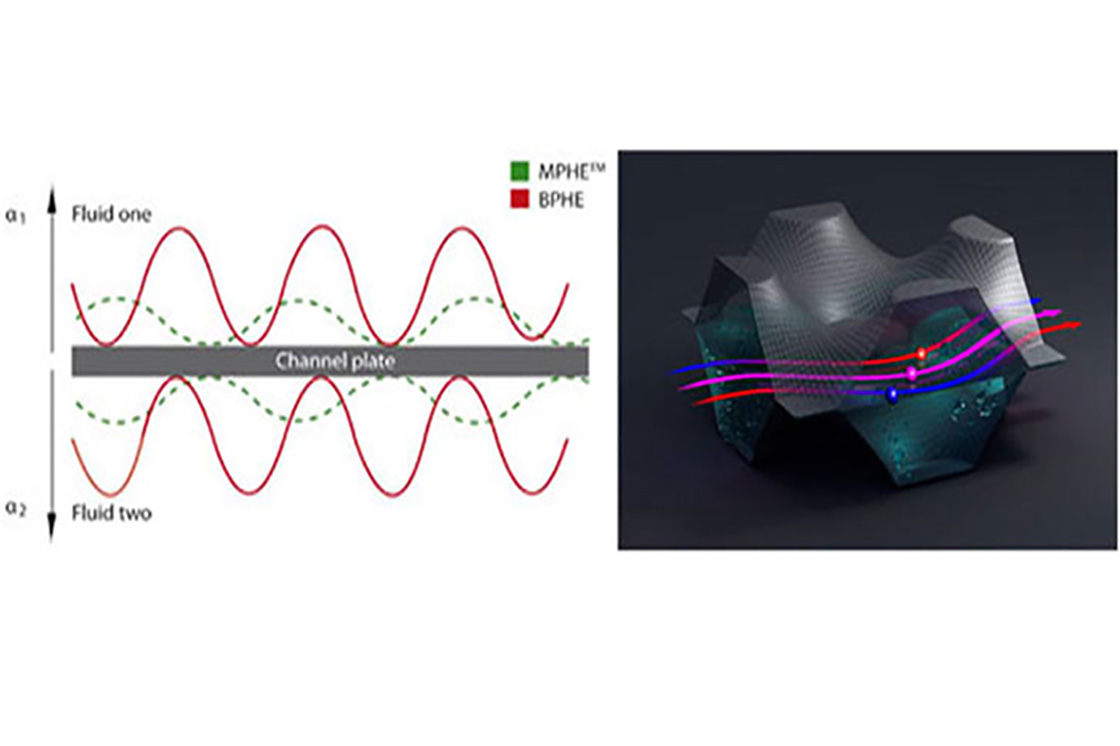
Traditional BPHEs have their brazing points in fixed, regular locations across the plates. In the MPHE, the position of each brazing point can be determined individually. This means brazing points can be concentrated in areas subject to higher mechanical forces. Strength is further increased by the dimples themselves, which offer a greater contact area (Fig. 4).
This freedom in the positioning of brazing points also offers opportunities to design solutions totally dedicated to the needs of different applications. Alongside the universal D-range models, Danfoss MPHEs are already available in two dedicated ranges: the H-range for heat pump applications and the C-range for chiller applications.
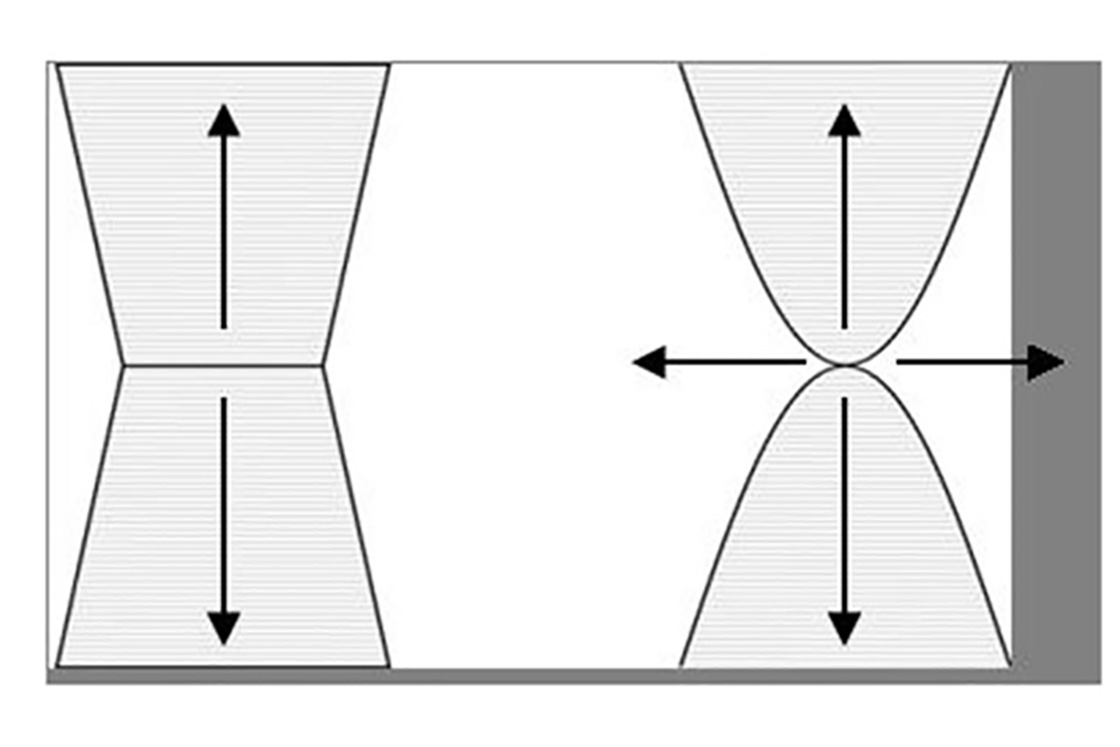
MPHE technology is completely changing the way we look at heat transfer in applications, making it possible for customers to penetrate new markets and deliver greater savings. Although the technology is universal across applications, early adopters have been concentrated in the heat pump and chiller segments. The efficiency gains from using Danfoss' H-range MPHEs in heat pumps are enabling manufacturers to increase profits as well as market share. In the chiller industry, which uses larger units, the C-range enables more economical solutions for both single- and dual-circuit systems.
An MPHE from Danfoss has a lower hold-up volume compared with traditional BPHEs. The heat exchanger is also simply smaller, reducing the refrigerant charge by up to 40%. This represents a core saving on the initial refrigerant charge, but of course the need for refills also has a significant impact on running costs. For a typical heat pump (60 kW), the savings on refrigerant amount to EUR 120 per year – before taxes.
The price of raw materials directly affects the price of heat exchangers, and forms an unwelcome part of many sales terms. The MPHE technology requires less raw material. So for a given capacity a lighter unit can be used. In turn, this makes the price of MPHEs less sensitive to increases in raw materials costs. For chillers, the value of the increased stability ranges from EUR 30 (160 kW) to EUR 55 (400 kW) annually.
You can explore these savings interactively for MPHEs in heat pump and chiller systems at bigexchange.danfoss.com.
The versatility of the MPHE's dimple technology offers great freedom in exploiting asymmetrical flows. MPHEs can achieve asymmetry ratios as high as 1:27, which allows the asymmetrical flow to be adapted precisely to the given operating conditions (Fig. 5).
Establishing the exact relationship between the two fluids in the heat exchanger is critical to creating asymmetrical solutions. MPHE technology offers high flexibility within its asymmetric envelope, making it possible to design exactly correct asymmetric flows for a given application and operating conditions. The efficiency of MPHEs with asymmetric flows has been verified in laboratory tests, and customer field tests show significant efficiency increases with the technology.
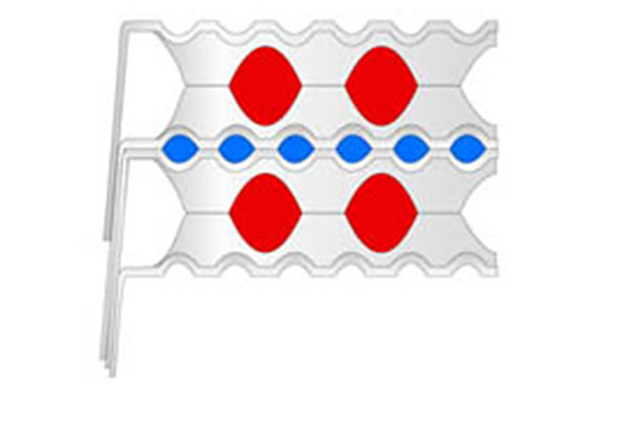
MPHE technology itself is unique, yet the MPHE is a safe choice. A Danfoss MPHE is manufactured in the same way as a traditional BPHE, following a well-proven manufacturing process. The same pressure vessel codes – including PED, UL/CSA and KHK – apply, and manufacturing is ISO 14000 (environment) and ISO 9001 (quality) certified. MPHEs are already the preferred technology for a number of leading European heat pump and chiller manufacturers (Fig. 6).
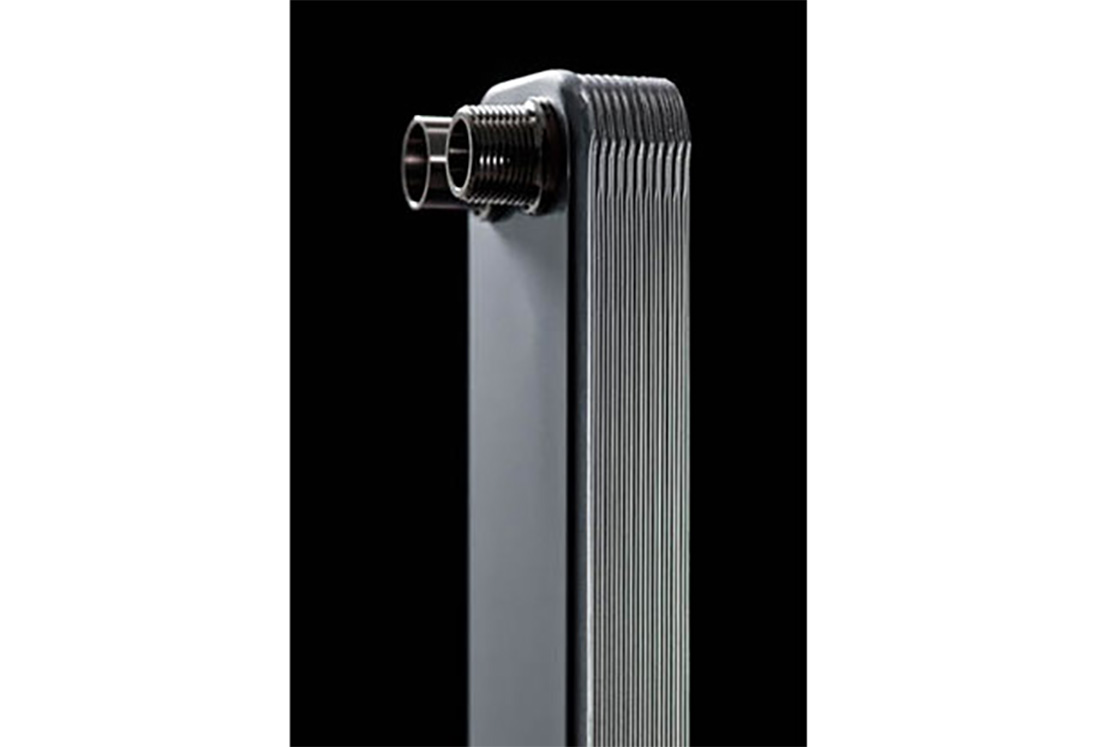