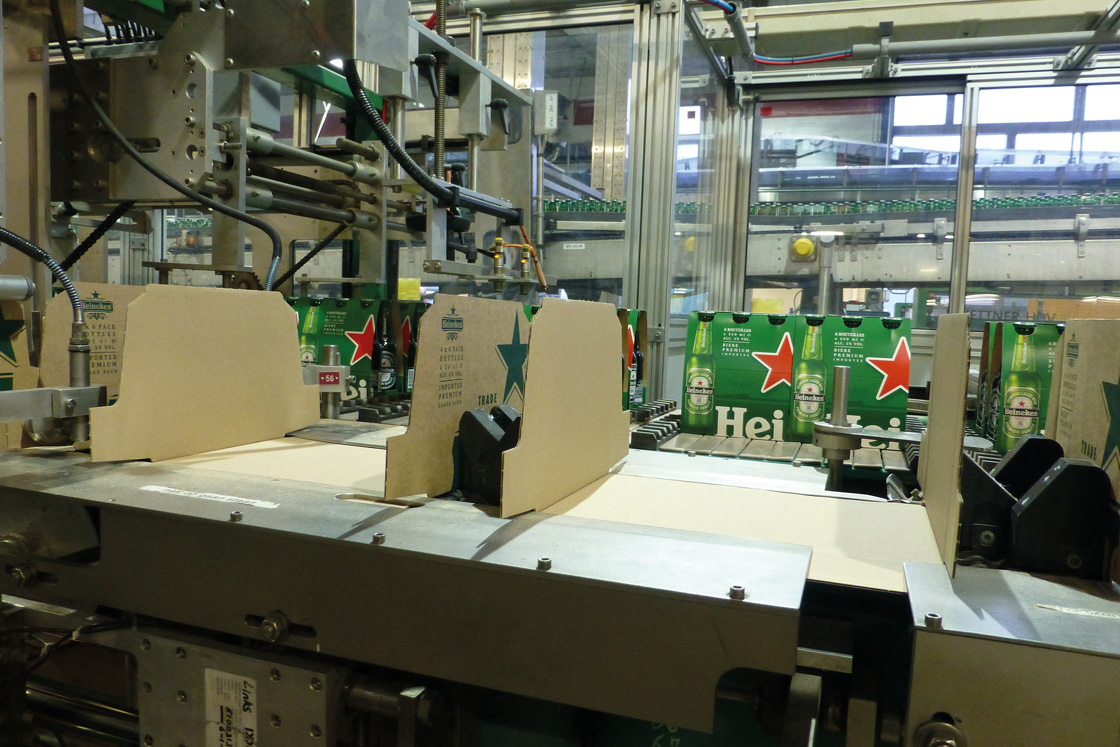
Sześć butelek piwa w kartonowym pudełku z uchwytem na górze. To takie proste! Ma to sens, ponieważ konsumenci często wybierają sześciopak. Firma Heineken w 's-Hertogenbosch w Holandii również lubi tę formę opakowania. Dzięki nowej linii do produkcji sześciopaków browar ten pakuje 44 000 butelek piwa w opakowania po sześć sztuk w ciągu godziny.
Widok z galerii nad halą pakowania jest imponujący. Dziesiątki metrów przenośników taśmowych przesuwa butelki piwa różnych marek w kierunku robotów i układarek. Po dotarciu na miejsce butelki znikają w mgnieniu oka we wszystkich rodzajach opakowań, w tym w wielu sześciopakach. Kilku operatorów przemieszcza się między liniami i interweniuje tylko wtedy, gdy dzieje się coś niepokojącego. Cisza podczas całego procesu jest po prostu niesamowita. Pakowanie w ciszy trwa zwyczajnie dalej.
Praca zespołowa rozwiązuje problem synchronizacji
Jednak linię do produkcji sześciopaków oparto na specjalnej technologii. W ciągu ostatnich dziewięciu miesięcy zespół firmy Heineken przy wsparciu firmy Danfoss pracował nad nowy układem napędowym i systemem sterowania dla tej linii pakowania.
Jan Brouwers, inżynier zajmujący się dopracowaniem szczegółów w zakładzie firmy Heineken w 's-Hertogenbosch, wspomina: „Największym wyzwaniem była synchronizacja wszystkich przetwornic. Poszczególne silniki o różnych mocach znamionowych, wahających się od 1,1 do 2,2 kW, wyposażone w różne przekładnie, musiały wszystkie znajdować się we właściwej pozycji w tym samym czasie. Z tego powodu zastosowaliśmy MCO 350, dodatkowy moduł do przetwornic serii VLT® dostarczony przez firmę Danfoss. Do zaprogramowania układu sterowania silnikami wykorzystaliśmy głównie sterownik PLC. Mogliśmy jednak wprowadzić synchronizację z samym modułem MCO 350. Moduł ten jest kartą dodaną do przetwornicy serii VLT®, która może być adresowana poprzez interfejs. Kiedy dotarliśmy już tak daleko, zaczęliśmy od jednej przetwornicy w danym momencie, a następnie dodawaliśmy kolejną przetwornicę, aż do momentu, gdy mieliśmy sześć przetwornic. Od tego czasu linia ta działa bez problemów. Nie musimy już stale jej obserwować. Największą korzyścią dla firmy Heineken jest większa niezawodność dostaw. W przeszłości nieplanowane wyłączenia utrudniały pakowanie. Teraz koniec z tym. Dzięki temu projektowi firma Heineken mianowała nas „Zespołem miesiąca”. Oczywiście takie uznanie jest zawsze mile widziane. Ale teraz wszyscy zajęliśmy się nowymi projektami. Wciąż przed nami tak wiele wyzwań, że na pewno nie będziemy się nudzić”.
Przetwornice serii VLT® standardowym rozwiązaniem od 1968
Dlaczego firma Heineken zdecydowała się na instalację przetwornic serii VLT® firmy Danfoss? Wyjaśnia Jan Brouwers: „Heineken i Danfoss współpracują od 1968 roku.
Oczywiście zaczęło się to już dawno temu, ale od tego czasu nasze firmy utrzymują stałe relacje. W pewnym momencie firma Heineken zdecydowała się rozpocząć stosowanie przetwornic serii VLT® firmy Danfoss jako rozwiązanie standardowe. Z jednej strony była to kwestia oszczędności kosztów, a z drugiej utrzymania jakości, wsparcia i niezawodności. Z czasem całe setki starszych przetwornic zostały zastąpione nowymi urządzeniami firmy Danfoss. I tak właśnie stało się tutaj, na tej linii pakowania, z której również schodzą sześciopaki”. 44 000 butelek na godzinę. Zaprojektowanie nowej linii pakowania wymagało naprawdę dużego wysiłku. Co trzeba było zrobić, aby to osiągnąć? Jan Brouwers wyjaśnia: „Wszelkie zmiany w istniejących urządzeniach muszą być dostosowane do bieżącej produkcji. Oznacza to, że nie możesz wykonywać czynności związanych z urządzeniami wtedy, kiedy chcesz. W sposób oczywisty danej linii dotyczą również określone wyzwania techniczne. Linia ta zawiera osiem silników, a wszystkim sterują przetwornice VLT® AutomationDrive FC 302. Silniki te tworzą układ napędowy dla przenośnika taśmowego i tackarki, głównego elementu tej linii. Tackarka składa tekturę i manipuluje butelkami, aby utworzyć sześciopak. Następnie tackarka układa cztery sześciopaki razem na tacy, nakłada na nie górną część i skleja pudełko. To pudełko zawiera 24 butelki, tak samo jak skrzynka. Nasza linia może teraz pakować 36 tac na minutę lub około 44 000 butelek na godzinę”.
Dalszych informacji udziela osoba kontaktowa:
Michael Kannekens, inżynier aplikacji oraz Kees Bolier, inżynier sprzedaży w firmie Danfoss B.V. Holandia