ÁFRICA DO SUL: A BMG Electronics usou os acionamentos Danfoss para dar suporte à DryTech International no desenvolvimento de um alimentador de rosca úmida exclusivo para uso em uma operação de platina que inclui mina, planta de processamento e fundição. Essa solução aumenta a confiabilidade com uma sincronização elegante e livre de controle de movimento servo, reduz custos e também facilita o tempo de manutenção.
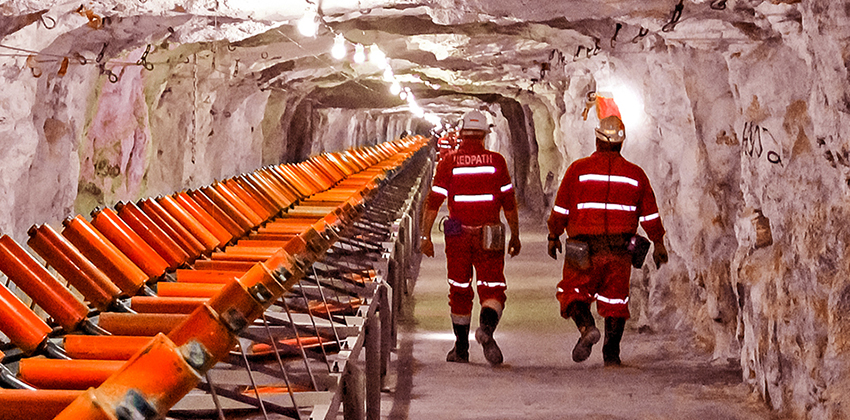
Saiba como a BMG Electronics usou os acionamentos da Danfoss para ajudar a DryTech International a desenvolver um alimentador de parafuso úmido excepcionalmente eficiente.
Desafio: Material incomum exige solução exclusiva
A DryTech International desenvolveu o alimentador de rosca úmida para essa fábrica para lidar com as características incomuns do material processado de metais do grupo da platina (PGMs), cromo e metais básicos. O material é extremamente pegajoso, com uma consistência semelhante à da argila, e precisava ser transferido suavemente para um secador. Além disso, esse material é recebido não apenas de minas dentro da área imediata na província de Limpopo, mas também de minas na província de Mpumalanga, na África do Sul, a mais de 300 km de distância. Durante o trânsito, alguns compostos secam, enquanto outros permanecem úmidos.
Do ponto de vista do projeto mecânico, as engrenagens necessárias para o alimentador seriam de grande porte, o que representaria alguns desafios práticos quando se tratasse de encaixar fisicamente na sincronização da unidade sem que os parafusos se chocassem. Engrenagens maiores também aumentariam substancialmente os custos dos alimentadores de rosca úmida. A facilidade de manutenção era outro requisito da fábrica. O rendimento necessário do primeiro alimentador de rosca úmida era de 30 a 40 toneladas por hora, com 15 toneladas por hora necessárias para o segundo alimentador.
Solução: Eixos de parafuso sincronizados
![]() |
![]() |
![]() |
Modelo 3D do alimentador úmido sem proteções | Modelo 3D do alimentador úmido com proteções | Configuração do alimentador de rosca úmida DryTech usando acionamentos FC 302 |
A DryTech construiu uma máquina experimental para testar a aplicação, e o teste mostrou que um eixo de três parafusos era a solução mais eficaz. Embora durante o teste os três eixos de rosca estivessem mecanicamente ligados uns aos outros, o cliente preferiu uma solução com eixos independentes, sincronizados eletronicamente usando unidades VLT® AutomationDrive FC 302 que controlam um motor/caixa de engrenagens de 22 kW em cada eixo. Esse foi um requisito essencial, pois os três eixos independentes precisam girar de forma coordenada para ajudar a evitar danos mecânicos. Por exemplo, se um dos motores, caixas de engrenagens ou eixos ficar sobrecarregado e desacelerar o motor, isso deve ser detectado por uma função de dessincronização e todos os eixos de parafuso devem parar. Depois que o problema for resolvido e o aplicativo voltar a funcionar manualmente, ele será automaticamente revertido para a posição sincronizada correta na inicialização, em vez de ser necessário retornar o eixo à posição inicial manualmente.

"A oferta do VLT® AutomationDrive FC 302 da Danfoss forneceu a solução ideal para esse cliente, devido à sua alternativa inovadora à abordagem tradicional de controle servo para operações de posicionamento e sincronização. Os inversores são adaptáveis às aplicações por meio de parametrização simples", explica Stephen Brown, gerente de desenvolvimento de negócios de mineração da Danfoss Turquia, Oriente Médio e África.
Durante a operação normal, a carga em cada inversor é relativamente leve - menos de 50% do torque de carga total do motor (FLT) - mas, devido à consistência pegajosa do material, há momentos em que ocorrem cargas mais altas. Isso se mostrou especialmente verdadeiro durante as condições de partida ou de baixa taxa de alimentação. Os acionamentos de 22 kW com motores de 22 kW são adequados para lidar com essas condições, pois combinam constantemente a potência com a carga. Os motores são montados acima da caixa de engrenagens, acionando cada eixo de parafuso, acionando a caixa de engrenagens por meio de uma correia de transmissão.
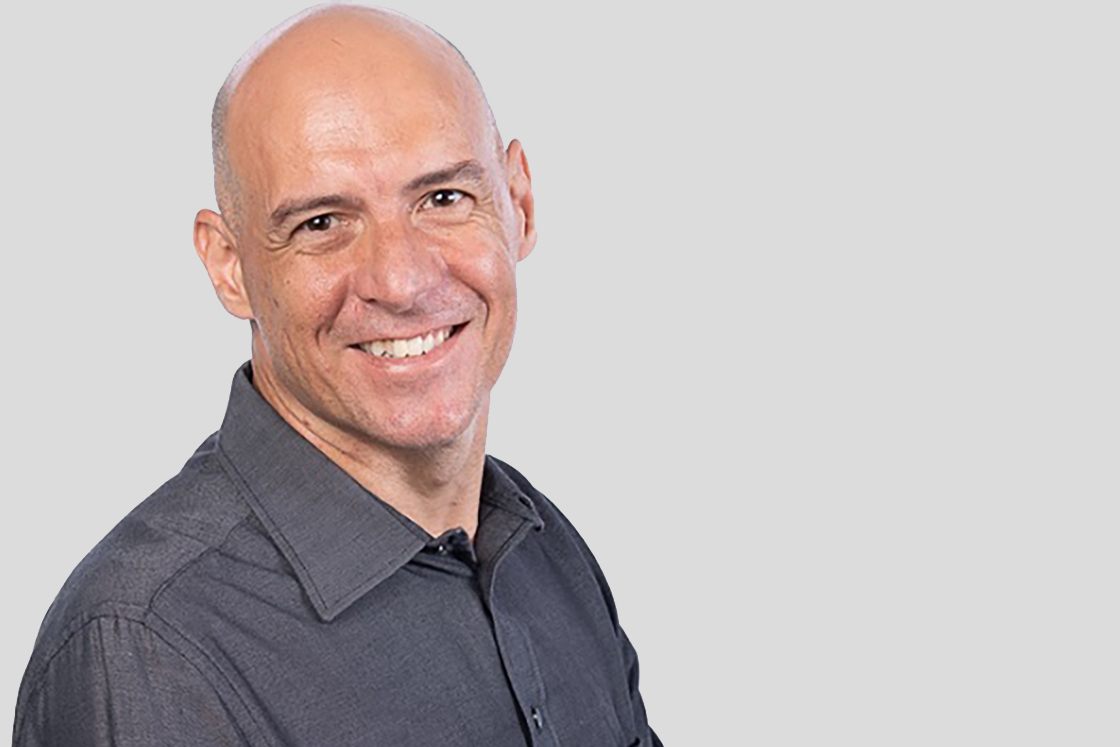
"Precisávamos de flexibilidade para poder ajustar a relação da polia da correia durante o comissionamento, a fim de definir a velocidade máxima e, portanto, a taxa de produção do alimentador. Isso também evita danos mecânicos na correia, que falhará primeiro."
- Riaan Van Niekerk, porta-voz da DryTech
Controle mais rígido de velocidade e operação
A aplicação final configurada por Juan Lerm, técnico de serviço de campo da BMG Electronics, compreende três parafusos conectados a motores de 22 kW e caixas de redução. O motor mestre (motor central) é controlado por um VLT® AutomationDrive FC 302 com PROFIBUS® e opções de codificador. O mestre PROFIBUS® é o sistema de controle da fábrica que controla a operação e a velocidade desse motor de acordo com os requisitos do processo. O motor mestre é equipado com um codificador para aumentar sua resposta de torque dinâmico, e o eixo desse motor tem um codificador de referência para medir a velocidade real de rotação do eixo do parafuso.
Quanto mais altos forem os pulsos por revolução (PPR), melhor será a sincronização, pois os incrementos são mais próximos uns dos outros, aumentando assim a resolução do feedback.
"Nessa aplicação, usamos codificadores absolutos multivoltas 8192 PPR", explica Mick Baugh, Gerente de Eletrônica, Divisão Eletromecânica, BMG. Quando o alimentador úmido precisa funcionar, ele dá um comando de "partida" para o acionador de velocidade variável (VSD) mestre via PROFIBUS®. Em seguida, o VSD mestre emite os sinais de partida para os VSDs seguidores."
Os dois parafusos seguidores são conectados ao VLT® AutomationDrive FC 302 com uma opção de controlador de sincronização VLT® MCO 350 também com PROFIBUS® para fins de monitoramento. O codificador mestre é conectado a ambos os MCOs como uma referência mestre, o que significa que os cartões MCO 350 monitoram a velocidade do eixo mestre. O codificador seguidor é instalado no eixo do parafuso dos parafusos seguidores, e esses codificadores são conectados a cada MCO respectivo como um sinal de feedback.
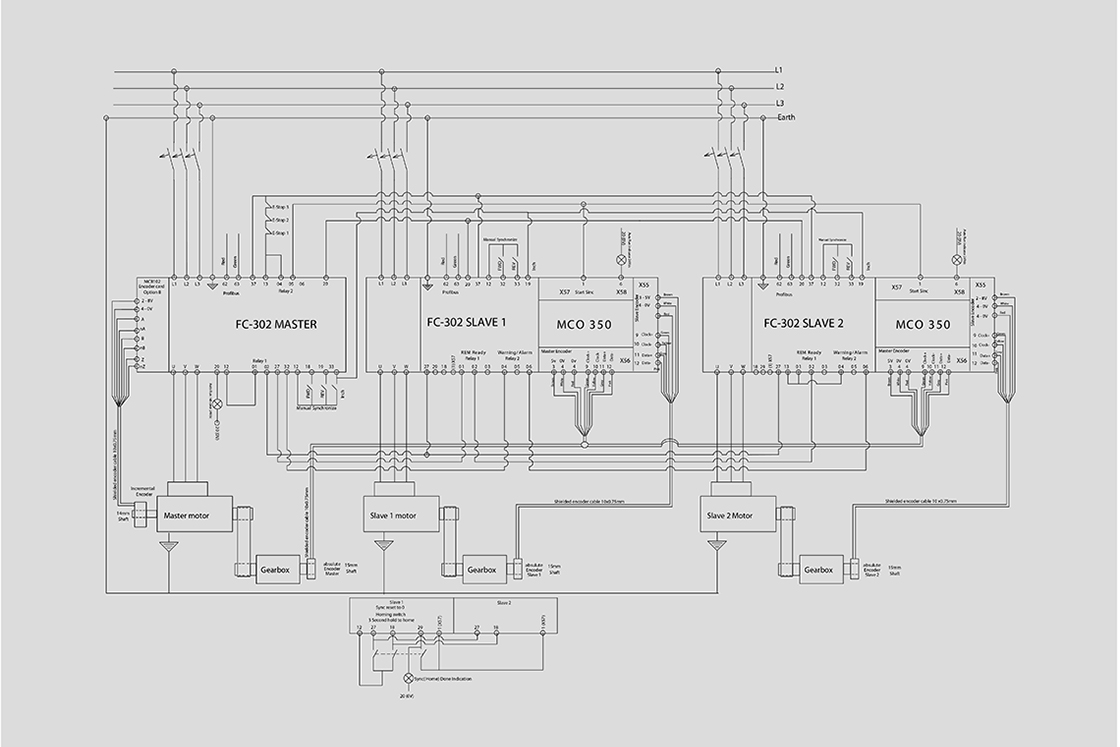
"A maneira como isso funciona é que o seguidor efetivamente espelha o codificador mestre: se o eixo do parafuso mestre for executado em uma determinada velocidade, o cartão MCO do seguidor monitora essa velocidade e a combina de modo que o eixo do seguidor seja executado em sincronia com a referência mestre", afirma Baugh.
"Se o aplicativo parar em um estado de alarme, todos os motores irão parar e os eixos seguidores ficarão fora de sincronia. Quando um comando de partida é dado, o VSD mestre tem um atraso de cinco segundos, de modo que os parafusos aumentam a velocidade e o aplicativo volta a se sincronizar sozinho. O mestre então aumentará a velocidade de referência de acordo com o sinal PROFIBUS®."
Se tiver sido feita manutenção no aplicativo, os parafusos ficarão fora de sincronia. Uma sincronização manual foi programada para que os VSDs entrem em uma segunda configuração, e agora cada parafuso pode ser deslocado para frente e para trás para colocar todos os parafusos novamente em uma posição de sincronia. Quando os parafusos estiverem corretamente alinhados, o técnico simplesmente pressiona o botão de sincronização para dar ao inversor uma nova posição zero. Quando o aplicativo for iniciado novamente, ele funcionará em sincronia.
"O fato de a opção MCO 350 do controlador de sincronização VLT® da Danfoss não exigir a gravação de um programa APOS especial também foi um fator decisivo significativo", acrescenta Baugh.
![]() |
![]() |
![]() |
Descubra as maneiras pelas quais os acionamentos inteligentes agregam valor às suas operações: VLT® AutomationDrive FC 302 |
Saiba mais sobre como aumentar a produtividade com a sincronização, o posicionamento e o controle de came da Danfoss | Descubra mais soluções de acionamento para economias significativas de CAPEX e OPEX em mineração e processamento mineral |
Visite a página da FC 302 | Leia o folheto sobre controle de movimento | Leia o folheto sobre mineração |
Aplicativos relacionados
-
if (isSmallPicture) {
; } else if (isBigColumns) { } else { }Drives para bombas em mineraçãoReduza a carga de calor da subestação e a infraestrutura de ar condicionado, com controle de bomba refrigerado a ar da Danfoss.
-
if (isSmallPicture) {
; } else if (isBigColumns) { } else { }Drives para transportadores em mineraçãoA flexibilidade para controlar a velocidade de transportadores longos pode ajudar a otimizar o sistema completo, reduzir os gargalos e prolongar a vida útil do motor.
-
if (isSmallPicture) {
; } else if (isBigColumns) { } else { }Drives para ventiladores de minasGaranta uma operação confiável e econômica dos ventiladores, tanto na superfície quanto subterrâneo, com fácil integração nos sistemas de ventilação sob demanda (VoD).
Estudos de Caso relacionados
-
if (isSmallPicture) {
; } else if (isBigColumns) { } else { }Economia de energia de 80 kW na mina KolomelaO resfriamento de canal traseiro nos VLT® AutomationDrives reduz a carga de calor da subestação, permitindo o uso de um sistema de ar-condicionado menor com menor consumo de energia.
-
if (isSmallPicture) {
; } else if (isBigColumns) { } else { }30% de redução de energia para a Yamana GoldOs inversores de frequência VACON® melhoram a operação de sistemas de ventilação e bombeamento subterrâneos e reduzem o consumo de energia de muitos processos de aplicação.