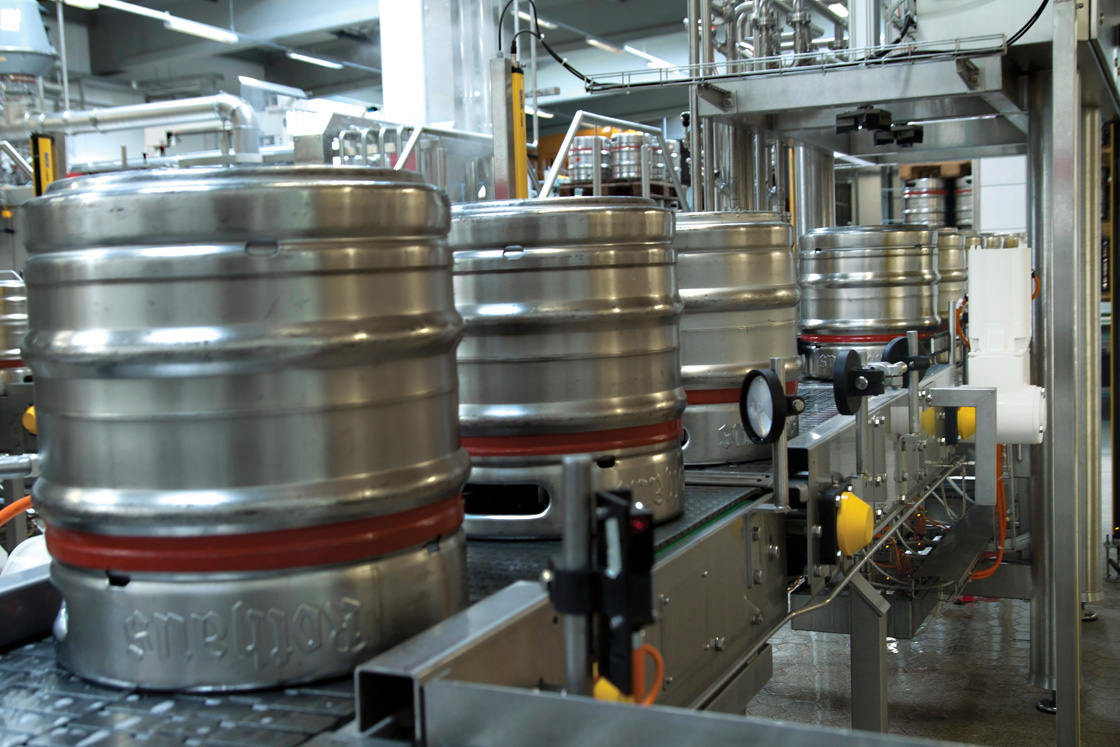
En installant une nouvelle ligne de remplissage de fûts avec des motoréducteurs VLT® OneGearDrive®, des convertisseurs de fréquence de la série VLT® AutomationDrive et des variateurs VLT® Decentral Drive, Rothaus AG a augmenté sa capacité de remplissage de 120 à 280 fûts par heure avec moins de types de variateurs et sans augmenter la consommation énergétique globale.
Tannenzäpfle, Eiszäpfle et Weizenzäpfle, pour ne citer que quelques-unes des bières bien connues produites par Badische Staatsbrauerei Rothaus AG, jouissent d'une excellente réputation parmi les amateurs de bière. L'image de marque, ainsi que la fille de la Forêt-Noire et les cônes d'épicéa de Norvège, constituent également des figures emblématiques au-delà des frontières du Bade-Wurtemberg. Fondé en 1791 à l'auberge « Zum Rothen Haus » par le prince-abbé Martin Gerbert II de l'abbaye bénédictine Saint-Blaise, le site figure parmi les brasseries les plus modernes d'Allemagne.
Si la qualité supérieure des produits était déjà la priorité absolue de la brasserie à l'époque, cette tradition s'est perpétuée au fil des ans. C'est pourquoi l'entreprise se concentre sur une hygiène optimale et des process de production avancés, et n'a pas manqué de réaliser d'importants investissements dans la technologie moderne des process depuis de nombreuses années.
Parmi les nouveautés, citons la salle de brassage, des cuves de fermentation et de stockage en acier inoxydable et une installation de tuyauterie de grande envergure. Les bières spéciales de la région de la Hochschwarzwald peuvent ainsi être produites selon des méthodes traditionnelles telles que la fermentation à froid et le vieillissement à froid prolongé dans des conditions d'hygiène optimales.
Expérience antérieure avec le potentiel d'économies éprouvé de Danfoss
Ralf Krieger, chef de projet, et Roger Jäger, responsable du remplissage, avec l'aide de leurs équipes, ont choisi les produits Danfoss pour les systèmes de variateur de la nouvelle usine.
« Nous utilisons les convertisseurs de fréquence Danfoss avec succès depuis plusieurs années et savions qu'il était possible de réduire le nombre de types de variateurs dans notre production. Le VLT® FlexConcept® nous aide également à réduire notre stock de pièces de rechange », explique Ralf Krieger, qui a également profité de l'occasion pour tester le Danfoss VLT® OneGearDrive®.
Le système de remplissage de fûts sert également de test pour la version hygiénique du VLT® OneGearDrive®.
« Bien que ces moteurs à aimant permanent (PM) ne soient pas absolument nécessaires dans l'usine, nous avons décidé d'en installer 25 dans la zone humide pour tester leur fonctionnement à long terme », poursuit-il. Les systèmes VLT® OneGearDrive® Hygienic sont commandés par 25 unités VLT® AutomationDrive FC 302, qui sont logées au centre d'une armoire électrique.
Automatisation totale du remplissage, du nettoyage à la palettisation
Le nouveau système de remplissage de fûts entièrement automatisé a été mis en service début 2011 en vue de remplacer un système obsolète. En raison d'investissements répétés et de la rénovation de l'installation, le chemin parcouru par la bière jusqu'à l'étape de remplissage n'avait eu de cesse de s'allonger dans l'ancienne installation. Désormais, la nouvelle ligne d'embouteillage s'intègre parfaitement dans la structure globale et réduit les distances à parcourir.
« La nouvelle ligne de remplissage est entièrement automatisée ; la seule tâche qui nécessite un effort manuel est d'acheminer les piles de palettes avec six fûts sur chaque palette à l'alimenteur à l'aide d'un empileur. Ensuite, les fûts en acier inoxydable, identifiés par des étiquettes RFID pour le contrôle qualité et le suivi, passent automatiquement à travers tout le système. Un robot retourne les fûts avec les vannes vers le bas et les place sur un convoyeur à bande. Les parois extérieures des fûts sont nettoyées, puis viennent ensuite les étapes de vidage et de pesage », explique Ralf Krieger.
Seuls les fûts complètement vides sont transférés sur les trois machines parallèles, fournies par l'entreprise de construction d'installations Albert Frey, pour les opérations de nettoyage interne approfondi, de rinçage et de stérilisation, et enfin de remplissage. Les fûts remplis sont retournés et équipés de couvercles en plastique marqués de toutes les données importantes, telles que le type, les ingrédients et la date de péremption, après quoi ils sont palettisés par un robot. Un transpalette automatique transporte ensuite les fûts fraîchement remplis de bières spéciales Rothaus sur palettes vers l'espace de stockage dédié de la brasserie.
Architecture du système
« Nous avons décidé de construire une architecture système centralisée dans la zone humide de l'usine, avec les convertisseurs de fréquence VLT® AutomationDrive FC 302 logés dans une armoire électrique centrale. Les unités modulaires ont été montées directement côte à côte pour une installation compacte », précise Ralf Krieger.
Les moteurs à induction standard dans la zone sèche du palettiseur sont commandés par 40 unités VLT® Decentral Drive FCD 300.
Les dimensions compactes des convertisseurs de fréquence facilitent leur installation sur site. Par ailleurs, ils sont équipés de couvercles pour assurer leur protection contre les chutes de fûts.
Les variateurs décentralisés sont recouverts d'un revêtement en poudre et sont donc faciles à nettoyer. Les ailettes de refroidissement inclinées et les surfaces lisses assurent un écoulement facile et fiable des liquides de nettoyage. Cinq diodes électroluminescentes indiquent à tout moment l'état du variateur et un afficheur connectable permet un diagnostic facile.
Composants intégrés gages d'efficacité
Le système Danfoss présente un autre avantage essentiel : tous les convertisseurs de fréquence Danfoss VLT® sont équipés en usine de filtres CEM et de selfs secteur comme composants intégrés. Il en découle un gain de place certain dans l'armoire, ce qui peut s'avérer utile dans des situations telles que la modernisation d'installations existantes, où l'espace est généralement limité.
L'effort de câblage est ainsi réduit et les convertisseurs de fréquence VLT® sont conformes aux limites en vigueur dans l'installation. Les filtres sont également pris en compte dans le calcul du rendement, qui s'élève à au moins 98 %. Dans la pratique, cela se traduit par une moindre dissipation de chaleur et permet un fonctionnement économe en énergie des variateurs. Le VLT® AutomationDrive FC 302 prend en charge de série les câbles moteurs longs, un aspect particulièrement utile dans les usines de boissons dont la structure système est centralisée. Il devient dès lors inutile de prévoir des filtres de sortie supplémentaires tant que la longueur du câble ne dépasse pas 300 mètres avec un câble non blindé ou 150 mètres avec un câble blindé, ce qui réduit encore davantage les coûts.
Coûts de l'énergie inchangés malgré l'augmentation de la production
La nouvelle solution a permis à Rothaus d'augmenter les capacités de remplissage de 120 à 280 fûts par heure avec des capacités de 10 à 50 litres. Et pourtant, force est de constater que l'usine, plus grande, ne consomme pas plus d'énergie qu'auparavant.
« Les composants utilisés dans le VLT® FlexConcept® ont fait leurs preuves dans l'usine jusqu'à présent. Tous les moteurs et convertisseurs de fréquence fonctionnent de manière fiable et leur conception offre de nombreux avantages par rapport aux variateurs traditionnels. L'équipement peut être exploité au choix dans une structure centralisée, décentralisée ou combinée. Tous les variateurs sont conçus pour un rendement énergétique extrêmement élevé et constituent un bon point de départ pour envisager d'autres projets avec les produits Danfoss », conclut Ralf Krieger.