With its robust production capacity and advanced agricultural and agro-processing capabilities, South Africa is Africa’s leading food and beverage industry market. The industry has shown a growing e-commerce segment and strong confectionery industry, with the country also taking the position of the twelfth largest consumer of beer in the world.
However, the local food and beverage sector has taken a knock over the COVID period, due to strict lockdown rules, growing unemployment levels and constrained consumer spending, with recent unrest also posing a threat to food security if these issues are not swiftly resolved.
The outbreaks in July this year notwithstanding, South African organisations are also subject to the same challenges as their global counterparts, says Ferdie Fortuin, sales manager – general industry at Danfoss Drives South Africa. Danfoss, a leader in food and beverage industry solutions, has an established footprint, both locally and worldwide, including industrial processing plants, food and beverage, packaging, cold storage, and refrigeration.
“In order to move forward, businesses within this sector need to ask themselves the difficult questions, for example, will their operation be able to handle the 60 to 70 percent increase in food production needed to meet population growth by 2050? Can they cope with a 27 percent increase in confectionary products demand by 2025, for instance? Or, from a food security point of view, can they help eliminate the 33 percent food loss that occurs during production, when more than 820 million people are going hungry globally?
“Will the dairy chain specifically be able to cope with surging requirements, with a 35 percent increase in milk demand forecasted by 2030? To put this into greater perspective, the International Farm Comparison Network’s (IPFN) Dairy Outlook Report describes a future scenario where the average cow will need to produce more than 20 percent more milk, putting pressure on dairy farms to increase output by over 50 percent,” Fortuin explains.
“In order to keep up with rapidly changing market dynamics and build greater resilience, transformative change is needed to allow food producers to scale up productivity, while at the same time bring down costs and improve efficiencies. All of this can be achieved by embracing the right technology.”
Industry 4.0 intelligent drives help change challenges into opportunities
In order to thrive in today’s world, food plants need to be able to scale up time and time again – quickly and efficiently - and one way of successfully executing this is through the use of intelligent drives.
“In the Industry 4.0 network, intelligent drives that feature smart sensors and predictive, preventative maintenance play a critical role,” he states. “This type of solution has proven to help cut 38 percent of energy wasted, boost food production by 60 percent, and eliminate 33 percent of food loss during the production process.”
Intelligent drives can connect securely to other elements within the network, including PLCs, sensors and the cloud, and also embrace the Bring Your Own Device (BYOD) concept to connect wirelessly to smart devices.
Danfoss powers food plants worldwide
While adding intelligence to a system can often be a complicated process, requiring additional sensors and components, a Danfoss intelligent drive already features smart built-in sensor technology. This means that it is able to act not only as a sensor, but also as a sensor hub and a controller, collecting data from both internal and external sensors.
“With Danfoss Drives’ built-in sensor technology, organisations can maximise efficiency while minimising waste, no matter the area of food production,” adds Fortuin. “And the first step towards increased productivity is predictive maintenance and condition-based monitoring.
“Through access to real-time data and condition-based monitoring, your drives can provide in-depth insight into equipment, monitoring health and predicting when faults will occur, making it possible to schedule planned maintenance at the most opportune times, and reducing downtime. This, in turn, allows for operational optimisation and deriving the greatest value from ingredients.”
In addition to predictive and condition-based monitoring, Danfoss drive solutions cater for the following applications:
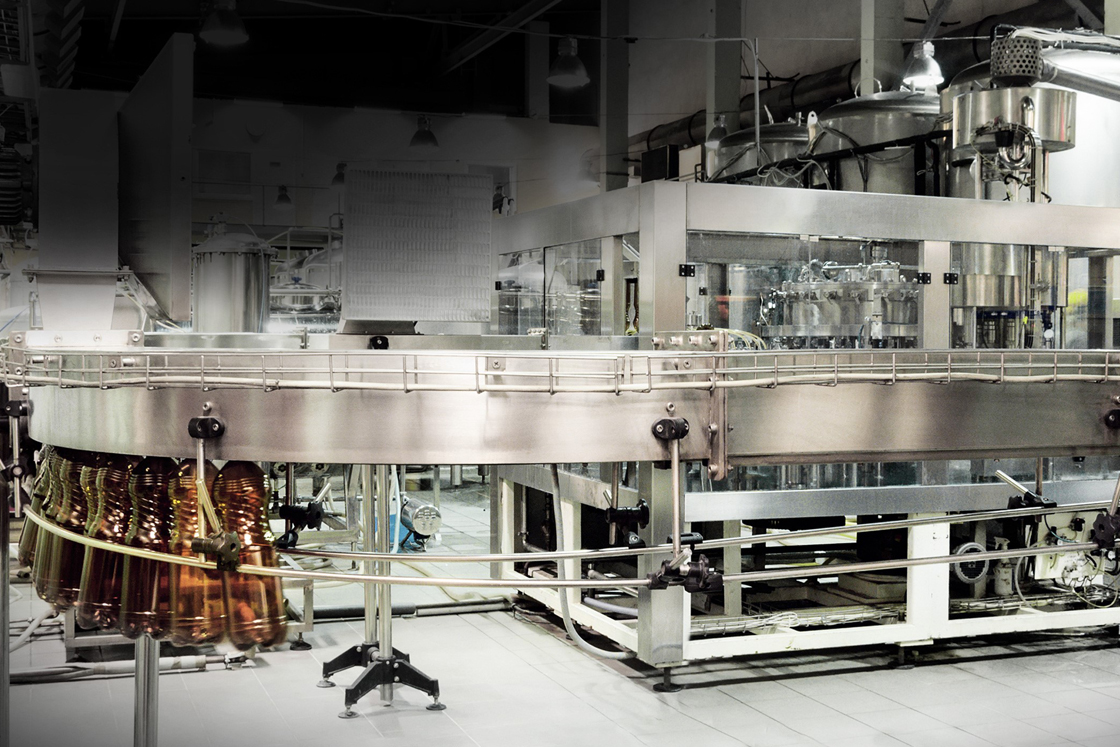
Position and synchronisation
To optimise performance, many applications in the food and beverage industry, such as conveyors, palletisers and packaging machines, need precise positioning and synchronisation. To date, these operations have been performed using servo drives. However, servo equipment is expensive, difficult to commission and requires additional cabling. The Danfoss Drives Integrated Motion Controller (IMC) is functionality configurable in the software of the VLT® AutomationDrive FC 302 that enables an AC drive to perform high-precision positioning and synchronisation operations without the need for additional modules or hardware.
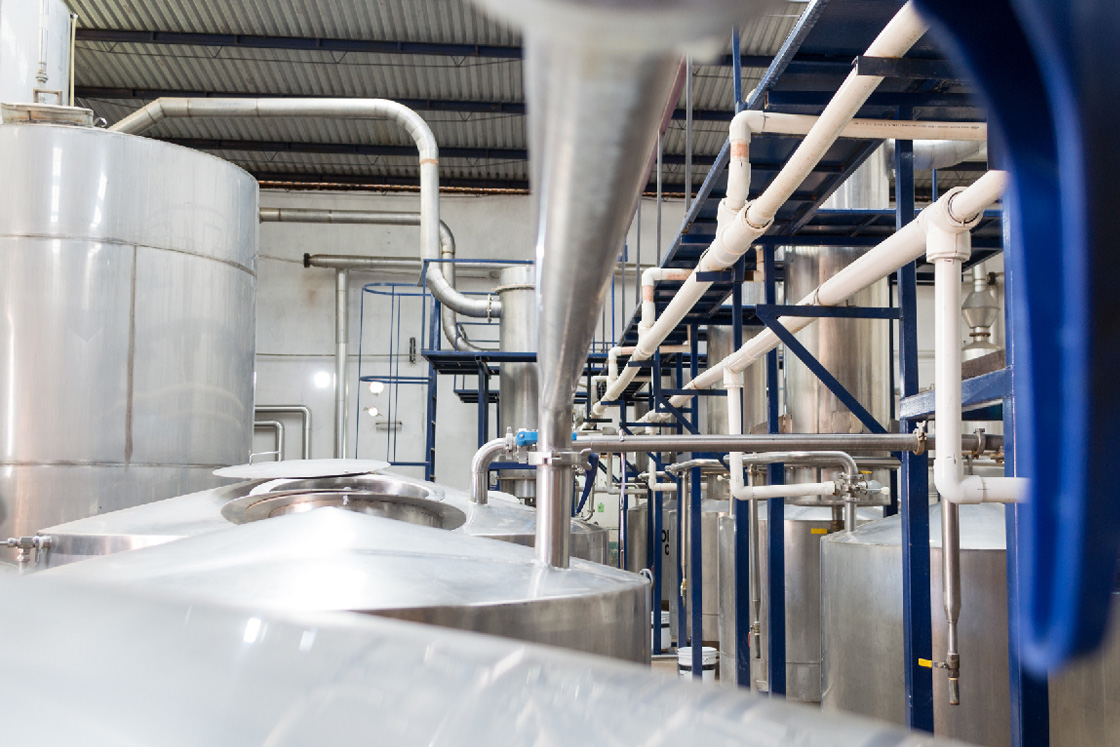
Pumps
By reducing the average speed of the pump motor from 100 to 80 percent, organisations can save 50 percent on energy consumed. Reducing the average speed by half increases the savings to 80 percent. As well as delivering these energy savings to an operation, implementing pump control with Danfoss drives can also dramatically reduce water consumption. Functionality such as the Cascade Controller distributes running hours evenly across all pumps, keeping wear and tear on individual pumps to a minimum and ensuring they continue to operate reliably. By optimising the combustion efficiency of boilers, electricity and fuel consumption can be curtailed. And the hydraulic performance of water-handling processes and the flow rate in feed water can be significantly improved by using AC drives.

Compressors
Danfoss drives enhance the control of compressors, reducing energy consumption and providing constant pressure regulation. Speed control is advantageous when an air compressor is running for long periods at part-load, and fewer starts and stops reduce mechanical wear. Hygiene requirements demand drives with robust enclosures that are able to withstand daily high-pressure wash-downs. Danfoss has a number of VLT® drives of varying sizes with IP66/UL Type 4X protection that can fulfil this need. Cascade configuration enables optimal interaction between compressor and drive under partial load. The base load is handled by a single compressor controlled by a VLT® Refrigeration Drive. When consumption rises, the drive starts up additional compressors one at a time. As a result, the compressors work largely at their optimum efficiency point, and the drive constantly maintains maximum energy efficiency throughout the system.

Conveyors
Conveyor applications need to perform reliably to ensure maximised uptime and the lowest cost of ownership. Danfoss solutions provide optimised motor control and, for example, improve quality and product consistency, and reduce waste. Highly sensitive products, such as still bottled water and alcohol-free beer or new materials for packaging and bottles, raise the hygiene requirements in production plants. Danfoss is unique in offering EHEDG and IPA certified solutions and products for use in hygiene-critical sub-systems. The VLT® FlexConcept® is currently the only solution on the market that provides EHEDG-certified components specifically intended for use in hygiene-critical sub systems. The system simplifies project planning, installation, commissioning and maintenance, especially for conveyor systems. System variants might be reduced by up to 70 percent, so users benefit from improved flexibility with a minimum number of modules, including motors and drives which offer a unified operating concept and standardised functionality, regardless of whether the system is implemented with a centralised or decentralised structure, in dry, wet or aseptic areas.
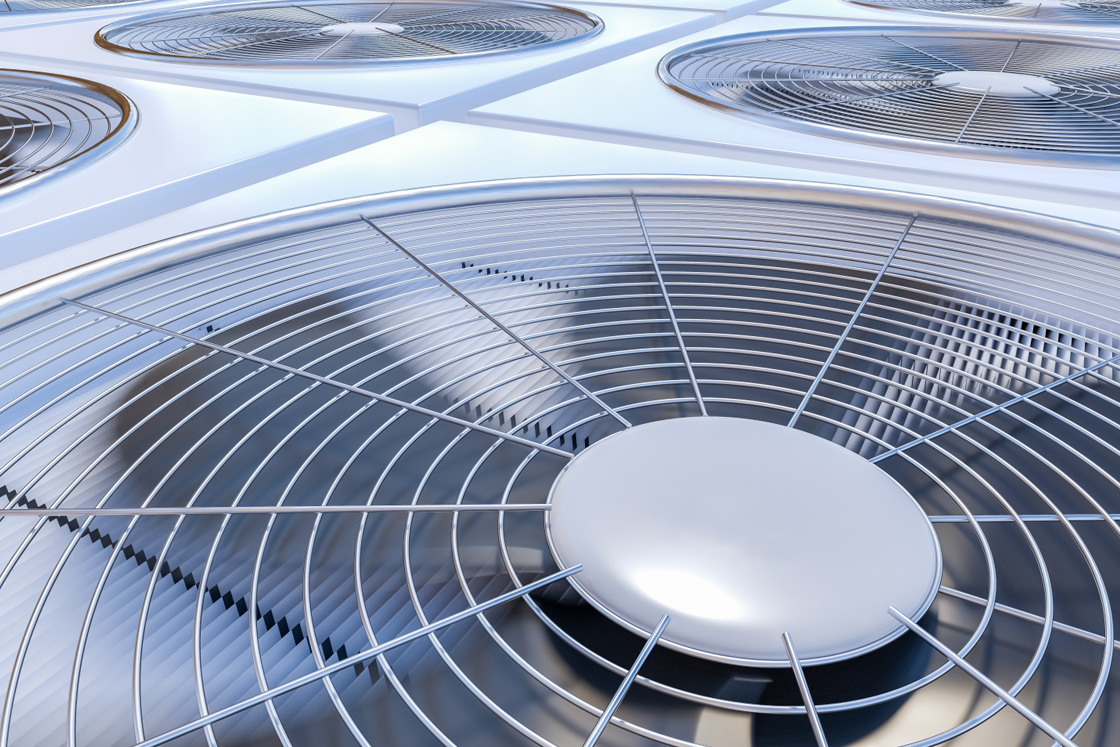
Fans
As energy becomes increasingly expensive, variable speed control of electrical motors has proven to be one of the most effective cost-reducing measures available. In addition to saving energy, fans benefit from dedicated drive features such as the ‘skip resonance’ function. This improves comfort levels by avoiding frequencies that create noise and damage. Reliable fan control can maintain specific air pressure and ensures a consistently hygienic environment for food and beverage operations. Condenser fan control gives a range of advantages including reduced charge of refrigerant, less build-up of dirt on the condenser, and the ability to run a floating setpoint for energy savings.
Danfoss intelligent drives also provide remote monitoring capabilities, keeping plants running efficiently, securely and accurately from anywhere.
“Danfoss is driving change across every food category, including confectionary and snacks; meat; bread and cereal products; dairy and eggs; vegetables; fish and seafood; convenience foods; fruit and nuts; baby food; spreads and sweeteners; spices and sauces; oils and fats; and pet food. As a business supporting critical infrastructure, we recognise that businesses within the food and beverage industry are exposed to additional risk as they keep operations running under today’s challenging circumstances, which include labour shortages, food security and panic-buying.
“Now more than ever, doing our part to help turn food production into a more intelligent process, keeping production lines up and running and unleashing the potential of food plants, is our priority,” Fortuin concludes.