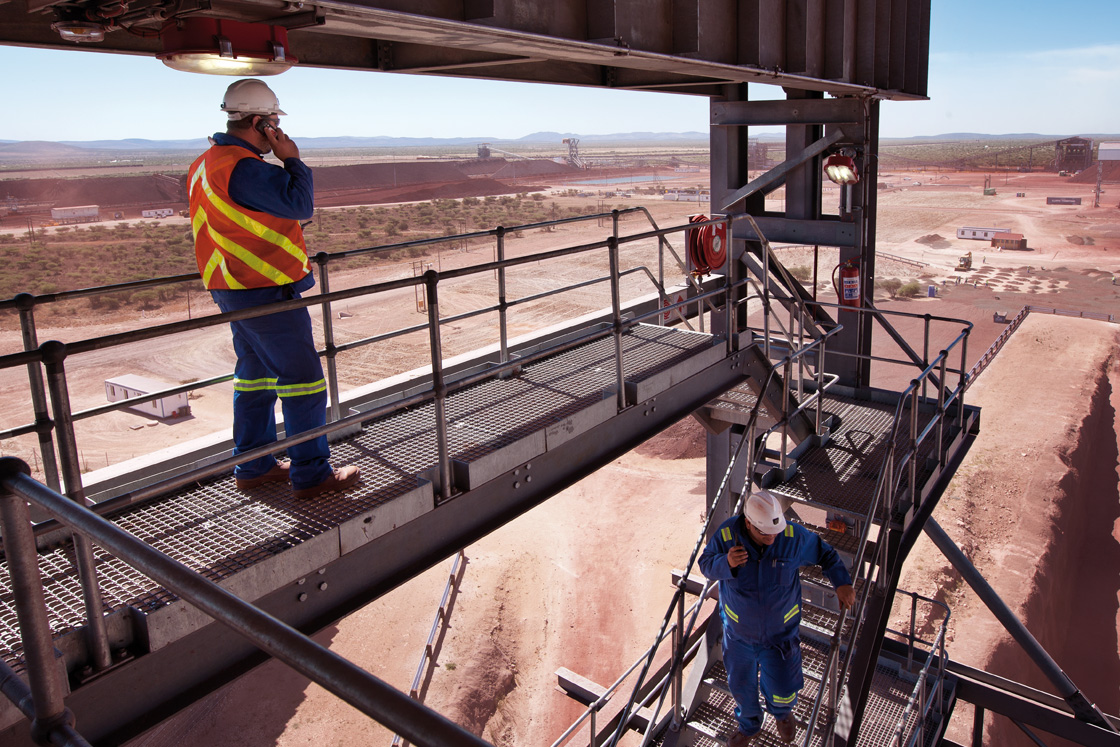
Utilizzando i convertitori di frequenza VLT® con canale di raffreddamento posteriore, la miniera risparmia circa 80 kW di energia elettrica. Questo vantaggio supera il risparmio energetico ottenuto utilizzando motori ad alto rendimento al posto dei motori ad efficienza standard in loco.
Installazione della sottostazione
Presso la miniera di minerali di ferro di Kolomela, in Sudafrica, sono stati installati tre convertitori di frequenza VLT® da 710 kW su un sistema di drenaggio della miniera che distribuisce acqua per il funzionamento dell'impianto e per l'approvvigionamento idrico della città locale.
Nell'industria mineraria sudafricana, la soluzione tradizionale è installare convertitori di frequenza in una sottostazione MCC chiusa per la protezione dai contaminanti minerari. Le miniere di minerali di ferro sono notoriamente ambienti molto polverosi, con particelle che raggiungono pochi micron. Questa polvere non è compatibile con l'elettronica e quindi l'aria dell'ambiente chiuso e controllato della sottostazione mantiene i convertitori di frequenza freschi e puliti. Tuttavia, per mantenere la corretta temperatura interna, il calore generato dai convertitori di frequenza deve essere eliminato dalla sottostazione da un condizionatore d'aria.
Carico del condizionamento aria ridotto
Il carico sull'impianto di condizionamento dell'aria, dovuto alla perdita di calore dei convertitori di frequenza e di altre apparecchiature della sottostazione, comporta normalmente un consumo di potenza relativamente elevato del condizionatore d'aria. Tuttavia, in questo caso, i convertitori di frequenza VLT® offrono la soluzione ideale, con il canale posteriore di raffreddamento integrato, che riduce significativamente il carico termico della sottostazione dovuto ai convertitori di frequenza. Utilizzando i convertitori di frequenza VLT® , il consumo di potenza della sottostazione si è ridotto di 80 kW,
- grazie alle minori perdite di calore dei convertitori di frequenza
- e ai minori carichi termici della sottostazione grazie al raffreddamento del canale posteriore
- con conseguente minore consumo di potenza dell'impianto di condizionamento dell'aria nella sottostazione.
Grazie al carico termico notevolmente inferiore, è stato possibile installare un impianto di condizionamento dell'aria più piccolo e più economico. Questo impianto ha un consumo di potenza e costi operativi inferiori.
Grazie al canale di raffreddamento posteriore di Danfoss, l'aria proveniente dall'esterno della sottostazione viene convogliata attraverso il pavimento della sottostazione, sospinta attraverso l'area del dissipatore VLT® e quindi espulsa dalla sottostazione tramite semplici condotti, senza influire sulla pressurizzazione della sottostazione.
Motori ad alta efficienza
Durante lo sviluppo della miniera, l'attenzione si è concentrata sull'ottimizzazione dell'efficienza energetica con tutti i mezzi possibili. Sono stati specificati motori ad alta efficienza per l'intero sito minerario, con un risparmio energetico stimato di 65 kW rispetto ai motori a efficienza standard. Tuttavia, il risparmio energetico di 80 kW generato dai soli convertitori di frequenza VLT® per il drenaggio delle miniere risulta superiore al risparmio totale ottenuto scegliendo motori ad alta efficienza.
Ammortamento
In una sottostazione mineraria, utilizzando convertitori di frequenza VLT® con canale posteriore di raffreddamento si ottengono risparmi annui sui costi energetici di esercizio pari a circa l'8–10% del costo totale di acquisto di tutti i convertitori di frequenza VLT®, rispetto all'utilizzo di convertitori di frequenza alternativi.
Il canale posteriore di raffreddamento richiede l'installazione di condotti aggiuntivi (e talvolta di filtri), ma a un costo inferiore rispetto all'assenza di canale posteriore di raffreddamento. Senza canale posteriore di raffreddamento si accumula nella sottostazione un carico termico significativamente più elevato, che comporta un impianto di condizionamento dell'aria più grande e più costoso e, di conseguenza, una bolletta elettrica più onerosa.
Pertanto, l'ammortamento per il canale di raffreddamento posteriore è istantaneo. La miniera realizza un risparmio netto dal primo giorno di attività.
Filtro senza manutenzione. Installalo e non ci pensi più per almeno dieci anni
A causa dell'ambiente difficile e polveroso della miniera di minerali di ferro di Kolomela, è necessario un filtro che ripulisca l'aria prima che entri nel canale del dissipatore del convertitore di frequenza VLT® .
Ciò che rende innovativa questa installazione di filtri dell'aria è l'uso di un sistema di filtri rotanti. Il filtro rotante utilizzato nelle condutture del canale posteriore di raffreddamento di questa sottostazione utilizza un effetto ciclone per fornire aria pulita in modo semplice e senza manutenzione.
L'alternativa è un filtro antiparticolato, che agisce bloccando il passaggio della polvere. I filtri antiparticolato sono tuttavia considerati inadatti per i siti di estrazione dei minerali di ferro perché si intasano a causa della polvere fine e richiedono quindi un elevato livello di manutenzione.
Ottimizzazione automatica dell'energia
Il sistema di pompaggio offre ulteriori risparmi utilizzando la funzione di ottimizzazione automatica dell'energia (AEO) del convertitore di frequenza. Attivando l'AEO si ottiene una magnetizzazione del motore sempre ottimale, in tempo reale, evitando un inutile consumo di energia.
Drives installati
In questo sito minerario, ai convertitori di frequenza delle pompe di drenaggio da 710 kW si affiancano molti altri convertitori di frequenza VLT, di potenza compresa tra 11 kW e 800 kW, per il controllo affidabile di apparecchiature come:
- trasportatori di alimentazione;
- trasportatori di scorte di buffer;
- trasportatori di stazioni di carico esterne per treni;
- motori di convertitori di frequenza a brandeggio e scorrimento su
- stabilizzatori per la ruota della benna,
- impilatori di minerali fini e
- impilatori di minerali grumosi.
La miniera Kumba Iron Ore di Kolomela comprende tre fosse a cielo aperto ed è un impianto di frantumazione e vagliatura a secco, situato vicino alla città di Postmasburg, nella provincia del Capo settentrionale del Sudafrica. L'impianto di lavorazione in cui sono installati i convertitori di frequenza VLT® è stato messo in funzione nel 2011. Nel 2013 la miniera di Kolomela ha prodotto 10,8 milioni di tonnellate di minerale di ferro, quasi 2 milioni di tonnellate in più rispetto all'obiettivo originario di 9 milioni di tonnellate. Il nome “Kolomela” significa “scavare più in profondità" o "perseverare”. Kumba Iron Ore, membro del gruppo Anglo American plc, è uno dei principali fornitori a valore aggiunto di minerale di ferro di alta qualità per l'industria dell'acciaio mondiale.