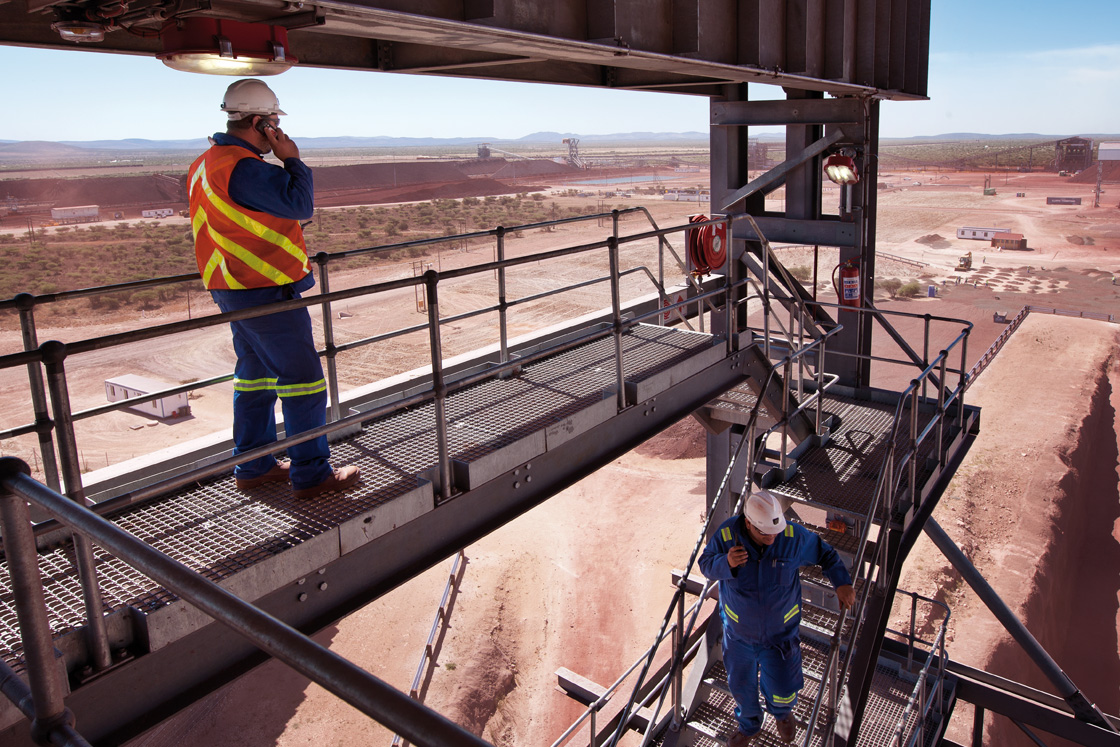
Mediante el uso de variadoresde frecuencia VLT® con refrigeración de canal trasero, la mina ahorra aproximadamente 80 kW de energía eléctrica. Este beneficio supera los ahorros de energía logrados mediante el uso de motores de alta eficiencia en lugar de motores de eficiencia estándar en el sitio.
Instalación de subestación
En la mina de mineral de hierro de Kolomela en Sudáfrica, se instalaron tres variadores de frecuencia VLT® de 710 kW en un sistema de drenaje de la mina que distribuye agua a las operaciones de la planta, así como al suministro de agua de la ciudad local.
La solución tradicional en la industria minera sudafricana es instalar variadores en una subestación MCC cerrada para protección contra contaminantes mineros. Se sabe que las minas de mineral de hierro son entornos particularmente polvorientos, con partículas de hasta unas pocas micras de tamaño. Este polvo no es compatible con la electrónica, por lo que el entorno de aire cerrado y controlado de la subestación garantiza que las unidades se mantengan frescas y limpias. Sin embargo, para mantener la temperatura interior correcta, el calor generado por los variadores debe eliminarse de la subestación mediante un acondicionador de aire.
Carga de aire acondicionado reducida
La carga en el sistema de aire acondicionado debido a la pérdida de calor de los variadores y otros equipos en la subestación normalmente da como resultado un consumo de energía relativamente alto del sistema de aire acondicionado. Sin embargo, en este caso, los convertidores de frecuencia VLT® ofrecen la solución ideal, con refrigeración de canal posterior integrada, que reduce significativamente la carga de calor de los convertidores en la subestación. Mediante el uso de convertidores de frecuencia VLT®, el consumo de energía en la subestación se redujo en 80 kW,
- debido a las menores pérdidas de calor de los convertidores
- menores cargas de calor en la subestación como
- resultado del enfriamiento del canal trasero
consiguiente menor consumo de energía del sistema de aire acondicionado en la subestación.
La carga de calor significativamente menor permitió la instalación de un sistema de aire acondicionado más pequeño y de menor costo. Este sistema tiene un menor consumo de energía y costos operativos.
Con el concepto de enfriamiento de canal posterior de Danfoss, el aire del exterior de la subestación MCC se canaliza a través del piso de la subestación, se sopla a través del área del disipador de calor VLT® y luego se expulsa de la subestación mediante conductos simples y sin afectar la presurización de la subestación.
Motores de alta eficiencia
Durante el desarrollo de la mina, la atención se centró en optimizar la eficiencia energética por todos los medios posibles. Se especificaron motores de alta eficiencia para todo el sitio de la mina, que se estima que proporcionan un ahorro de energía de 65 kW en comparación con los motores de eficiencia estándar. No obstante, los ahorros de energía de 80 kW generados por los convertidores de frecuencia VLT® para achique de minas por sí solos equivalen incluso a más que los ahorros totales obtenidos al seleccionar motores de alta eficiencia.
recuperación
En una subestación de mina, el uso de variadores de frecuencia VLT® con refrigeración de canal posterior suele generar ahorros anuales en costes operativos de energía que equivalen aproximadamente al 8 %-10 % del coste total de compra de todos los variadores de frecuencia VLT®, en comparación con el uso de convertidores alternativos.
Aprovechar el enfriamiento del canal posterior requiere la instalación de conductos adicionales (y, a veces, filtros), pero esto se puede lograr a un costo menor que no usar el enfriamiento del canal posterior. Sin refrigeración de canal trasero, se acumula una carga de calor significativamente mayor de los variadores en la subestación, lo que requiere la compra de un sistema de aire acondicionado más grande y más costoso, y una factura de energía más alta.
Por lo tanto, la recuperación de la inversión en el enfriamiento del canal posterior es instantánea. La mina logra un ahorro neto desde el primer día de operaciones.
Filtro sin mantenimiento. Instalarlo e ignorarlo durante diez años o más
Debido al entorno duro y polvoriento de la mina de mineral de hierro de Kolomela, se requiere un filtro de aire para limpiar el aire antes de que entre en el canal del disipador de calor del convertidor de frecuencia VLT®.
Lo que hace que esta instalación de filtro de aire sea innovadora es el uso de un sistema de filtro giratorio. El filtro giratorio utilizado en el sistema de conductos de refrigeración del canal trasero de esta subestación utiliza un efecto ciclónico para proporcionar una solución de aire limpio, sencilla y sin mantenimiento.
La alternativa es un filtro de aire de partículas, que actúa bloqueando el paso del polvo. Sin embargo, los filtros de aire de partículas se consideran inadecuados para las minas de mineral de hierro porque se obstruyen debido al polvo fino y, por lo tanto, requieren un alto nivel de mantenimiento.
Optimización automática de energía
El sistema de bombeo ofrece ahorros adicionales al utilizar la función de optimización automática de energía (AEO) del variador. La activación de AEO garantiza que la magnetización del motor esté siempre en el requisito óptimo en tiempo real y que no se gaste energía innecesariamente.
Unidades instaladas
Además de los variadores de bomba de achique de 710 kW en esta mina, hay muchos otros variadores VLT clasificados entre 11 kW y 800 kW, que controlan de manera confiable equipos que incluyen:
- Transportadores de alimentación
- Transportador de almacenamiento intermedio
- Transportador de la estación de carga del tren
- Motores impulsores de giro y largo recorrido en recuperador de rueda de cangilones, apilador de mineral fino y apilador de minerales grumosos
La mina Kolomela de Kumba Iron Ore consta de tres pozos a cielo abierto y es una operación completa de trituración en seco y criba, situada cerca de la ciudad de Postmasburg en la provincia de Northern Cape en Sudáfrica. La planta de procesamiento donde están instalados los variadores VLT® se puso en marcha en 2011. Durante 2013, la mina Kolomela produjo 10,8 Mt de mineral de hierro, casi 2 Mt por encima del objetivo original de 9 Mt. El nombre “Kolomela” significa “cavar más profundo o más lejos, perseverar”. Kumba Iron Ore, miembro del grupo Anglo American plc, es un proveedor líder de valor agregado de mineral de hierro de alta calidad para la industria siderúrgica mundial.