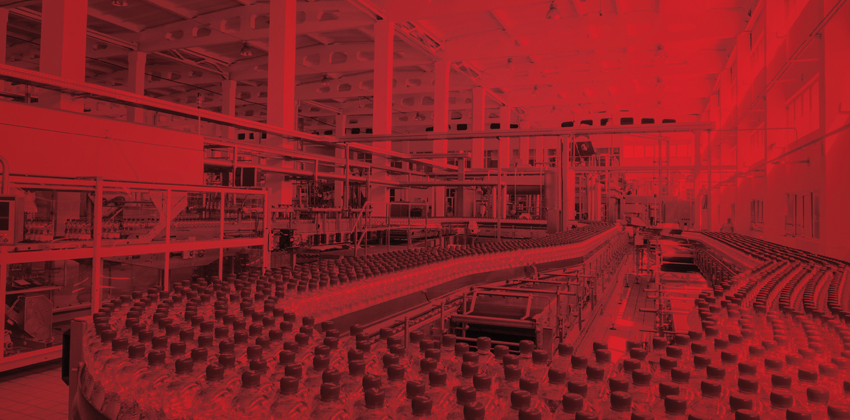
Въведение
Днес задвижванията са повече от обикновени захранващи процесори. Със способността си да действат като сензори и сензорни концентратори, да обработват, съхраняват и анализират данни, заедно с възможностите за свързване, задвижванията са жизненоважни елементи в съвременните системи за автоматизация. Интегрираната функция за наблюдение, базирана на състоянието, дава възможност за нови начини за извършване на поддръжка, като поддръжка, базирана на моментното състояние.
Еволюция на системите за индустриална автоматизация
В прехода към настоящото хилядолетие станахме свидетели на дълбока промяна в технологиите, която доведе до изцяло нов начин на работа в дигиталния свят. Това е четвъртата индустриална революция. Първата индустриална революция, която се случи през 18-ти и 19-ти век, е Механична революция, предизвикана от изобретяването на парната машина. До края на 19-ти и началото на 20-ти век се разгръща втората индустриална революция с приемането на масовото производство, електрификацията и промените в комуникациите. Този период се нарича още Електрическата революция. По-късно през 20-ти век, третата индустриална революция донесе напредък в полупроводниците, компютрите, автоматизацията и интернет. Тази фаза е известна още като Цифрова революция. Четвъртата индустриална революция се появи в резултат на свързването на компютри, хора и устройства в мрежа, подхранвани от данни и машинно обучение. Въпреки че терминът „Индустрия 4.0“ е доста неясен, възможна дефиниция за Индустрия 4.0 описва интелигентното свързване в мрежа на хора, устройства и системи чрез използване на всички възможности за дигитализация в цялата верига на добавената стойност.
Тенденции в системите за автоматизация на Индустрия 4.0
Въздействието на Индустрия 4.0 върху двигателните системи е миграция от „пирамидата за автоматизация“ към „мрежови системи“. Това означава, че различните елементи на системата, като двигатели, задвижвания, сензори и контроли, са свързани помежду си и свързани с облак – център за данни, където данните се съхраняват, обработват, анализират и се вземат решения.
Надпис: Пирамида за автоматизация
Надпис: Мрежа за автоматизация
В една мрежа за автоматизация количеството данни е важно. Тъй като данните се получават основно от сензори, броят на сензорите в съвременните системи за автоматизация се увеличава. Двигателите и задвижваните машини като вентилатори, помпи и конвейери не са най-очевидните участници в мрежата за данни. Следователно сензори трябва да събират данни от тези машини. Сензорите са свързани към мрежата за данни с помощта на различни средства за използване на данните. По време на въвеждането на усъвършенствана система за наблюдение на състоянието, допълнителните разходи за сензори и свързаност често се разглеждат като бариера.
Съвременните задвижвания с променлива скорост отварят нови възможности в мрежата за автоматизация на Индустрия 4.0. Традиционно задвижванията се считат за мощни процесори за контролиране на скоростта на двигателя. Днес задвижванията с променлива скорст също са част от информационната верига, използвайки предимството на вградената процесорна мощност, капацитет за съхранение и комуникационен интерфейс в устройството.
Какво е интелигентно задвижване?
В Индустрия 4.0 задвижването играе важна роля и се характеризира с някои активни функции:
- Сигурна свързаност: Устройството за регулиране на скоростта може да се свързва с други елементи по сигурен начин. Други елементи в мрежата могат да включват устройства, PLC, сензори и облак.
- Задвижването действа като сензор: Задвижването използва анализ на тока и напрежението на двигателя, за да усети работата на двигателя и приложението.
- Задвижването действа като сензорен хъб: Устройството получава данни от външни сензори, свързани с процеса, който се контролира от задвижването.
- Задвижването действа като контролер: Устройството може да замени PLC, където приложението го позволява.
- Дайте своя собствена концепция за задвижването: Безжична връзка със смарт устройства (смартфон, таблет).
Информацията от устройството може да бъде идентифицирана по следния начин:
- Моментни сигнали: Сигнали, които се измерват директно от задвижването с помощта на вградени сензори. Данни като ток на двигателя, напрежение, температура на задвижването и тяхната производна, която е мощност като умножение на ток и напрежение или въртящ момент на двигателя. Освен това задвижването може да се използва като хъб за свързване на външни сензори, които осигуряват мигновени сигнали.
- Обработени сигнали: Сигнали, които са получени от мигновените сигнали. Например статистическо разпределение (максимални, минимални, средни и стандартни отклонения), анализ на честотната област или индикатори за профила на мисията.
- Аналитични сигнали: Сигнали, които предоставят индикации за състоянието на задвижването, двигателя и приложението. Сигналите се използват за задействане на поддръжка или за довеждане до подобрения в дизайна на системата.
Техниките за анализ на характеристиките на тока на двигателя позволяват на задвижването да наблюдава състоянието на двигателя и приложението. Техниката позволява потенциално да се елиминират физически сензори или да се извлекат ранни сигнатури за повреда, които може да не са били възможни. Например, използването на техниката дава възможност да се открият предварително неизправности на намотката или ексцентриситет на механичния товар.
Концепцията на устройството като сензорен хъб включва свързване на външни сензори към устройството, като по този начин се спестява необходимостта от шлюз за свързване на физическия сензор към мрежата за данни. Сензори за вибрации, сензори за налягане и температурни сензори са примери за сензори, които могат да бъдат свързани към задвижването. Предимството на концепцията не е свързано само с цената, но и позволява корелацията на данните от сензора с различни видове данни, налични в устройството. Очевиден пример е корелацията на нивото на вибрация от външен сензор със скоростта на двигателя, тъй като вибрациите са зависими от скоростта.
Поддръжка, базирана на състоянието
Техниките за анализ на характеристиките на тока на двигателя позволяват на задвижването да наблюдава състоянието на двигателя и приложението. Техниката позволява потенциално да се елиминират физически сензори или да се извлекат ранни сигнатури за повреда, които може да не са били възможни. Например, използването на техниката дава възможност да се открият предварително неизправности на намотката или ексцентриситет на механичния товар.
Концепцията на устройството като сензорен хъб включва свързване на външни сензори към устройството, като по този начин се спестява необходимостта от шлюз за свързване на физическия сензор към мрежата за данни. Сензори за вибрации, сензори за налягане и температурни сензори са примери за сензори, които могат да бъдат свързани към задвижването. Предимството на концепцията не е свързано само с цената, но и позволява корелацията на данните от сензора с различни видове данни, налични в устройството. Очевиден пример е корелацията на нивото на вибрация от външен сензор със скоростта на двигателя, тъй като вибрациите са зависими от скоростта.
Защо е необходима поддръжка, базирана на състоянието?
Коригиращата и превантивната поддръжка са базирани на неизправност (събитие) или на време. Следователно поддръжката се извършва в случай на неизправност(и) (коригиране) или след предварително определени работни часове (превантивно). Тези видове поддръжка не използват обратна връзка от действителното приложение.
С въвеждането на Индустрия 4.0 и наличието на данни от сензори, вече е възможна поддръжка, базирана на моментното състояние и прогнозиране. Такива стратегии за поддръжка използват действителни данни от сензори, за да определят състоянието на оборудването в експлоатация (поддръжка, базирана на състоянието) или за прогнозиране на бъдещи повреди (прогнозна поддръжка).
Преглед и предимства
Поддръжката, базирана на състоянието, е най-лесната и интуитивна техника за поддръжка, базирана на данни от действителното приложение. Получените данни се използват за наблюдение на изправността на оборудването в експлоатация. За тази цел се избират ключови параметри като индикатори за идентифициране на развиващи се дефекти. Състоянието на част от оборудването обикновено се влошава прогресивно. Това се илюстрира от P-f кривата, която показва типичен модел на ескалция на повредата. Функционална повреда възниква, когато оборудването не изпълнява предназначената функция. Идеята на поддръжката, базирана на състоянието, е да се открие потенциалната повреда, преди да възникне действителна повреда.
Надпис: P-f крива, изобразяваща типичен модел на деградация
В този случай планирането на действия по поддръжката предоставя много предимства като:
- Намаляване на времето за престой
- Елиминиране на неочаквани спирания на производството
- Оптимизация на поддръжката
- Намаляване на запасите от резервни части
Функции за наблюдение на състоянието за задвижвания с променлива скорост
Неразделна част от поддръжката, базирана на състоянието, включва наблюдение на състоянието на оборудването. При приложения с променлива скорост състоянието на приложението често зависи от скоростта. Например, нивата на вибрации са склонни да се повишават при по-високи скорости, въпреки че тази връзка не е линейна. Всъщност резонансите могат да възникнат при определени скорости и след това да изчезнат, когато скоростта се увеличи.
Използването на независима система за наблюдение на състоянието на приложение с променлива скорост се усложнява от необходимостта от познаване на скоростта и корелирането на наблюдаваната стойност със скоростта. Използването на задвижвания за мониторинг на състоянието („задвижване като сензор“ или „задвижване като сензорен концентратор“) е изгодно решение, тъй като информацията за скоростта на приложението вече присъства в задвижването. Освен това информацията за натоварването/въртящия момент на двигателя и ускорението е лесно достъпна в задвижването.
Мониторингът на състоянието следва процедура от три стъпки:
1. Установяване на базова линия
2. Определяне на прагове за предупреждения и аларми
3. Извършване на наблюдението.
1. Установяване на базова линия
За да е ефективна една система за наблюдение на състоянието, първата важна стъпка е да се определят и дефинират нормалните работни условия. Установяването на базова линия означава да се дефинира нормалното работно състояние за приложението, което се нарича базово. Има няколко начина за определяне на базовите стойности.
Ръчна базова линия: Когато базовите стойности са дефинирани чрез предишен опит, познатите стойности се програмират в задвижването.
Изходна линия: Базовата линия може да бъде определена по време на въвеждане в експлоатация. Използвайки този метод, се извършва преглед на скоростта през съответния диапазон на скоростта, определящ състоянието във всяка точка на скоростта. Въпреки това, в определени сценарии по време на въвеждане в експлоатация е възможно приложението да не работи с пълен капацитет или да е необходим период на износване. В тези ситуации базовият цикъл трябва да се извърши след периода на износване, за да се улови работно състояние, което е възможно най-близо до нормалните операции.
Онлайн базова линия: Това е усъвършенстван метод, който улавя базовите данни по време на нормална работа. Това е полезно в ситуации, когато базово изпълнение не може да се извърши, тъй като приложението не позволява изследване на целия диапазон на скоростта. След установяване на базовата линия, следващата стъпка е генериране на прагове за предупреждения и аларми. Праговете показват състоянието на приложението, по време на което потребителят трябва да бъде уведомен. Има различни начини за индикация на състоянието на оборудването и един от най-популярните в индустрията е състоянието на светофара с четири цвята, което е описано в спецификацията на VDMA 24582 Fieldbus неутрална справка за наблюдение на състоянието във фабричната автоматизация.
Цветовете означават следното:
Зелено: Показва, че оборудването е в добро състояние и работи ефективно.
Жълто: Показва етап на предупреждение 1 и означава, че първият праг е надвишен. Действие по поддръжката може да бъде планирано от обслужващия персонал.
Оранжев: Показва предупреждение 2 или критичен етап и означава, че вторият праг е надвишен. Незабавните действия по поддръжката трябва да се извършват от обслужващия персонал.
Червено: Показва аларма и означава, че машината ще спре и е необходима коригираща поддръжка.
2. Определяне на прагове за предупреждения и аларми
Следните методи се използват за дефиниране на прагови стойности:
- Абсолютно: Това е често срещаният метод, когато стойностите на оборудването вече са известни. Прагът има фиксирана стойност, независимо от измерената базова стойност. Например, когато операторът знае абсолютната граница за оборудването, се задава абсолютна стойност за алармен праг. В случай на мониторинг на вибрациите, граничните стойности, описани в стандарти като ISO 10816/20816, могат да се използват за алармен праг като абсолютна стойност.
- Отместване: Методът за задаване на праговите стойности изисква разбиране на приложението и базовите стойности. Прагът зависи от базовата стойност, до която е избрано дефинирано от потребителя изместване. Рискът в този случай е задаване на много ниска или висока стойност, водеща до фалшиви положителни резултати. Фалшивите настройки могат да доведат до неотзивчив мониторинг, дори в случай на неизправности.
- Фактор: Този метод е по-лесен за използване от изместването, защото изисква по-малко разбиране на приложението. Прагът зависи от базовата стойност, която се умножава по коефициент. Например, праговата стойност може да бъде 150% от изходното ниво. Рискът в този случай е поставянето на много висок праг.
3. Извършване на наблюдението
Мониторингът се извършва с непрекъснато сравнение със зададените праговете. При нормална работа действителните стойности се сравняват с праговата стойност. Когато наблюдаваните параметри надхвърлят праг за предварително определено време, се активира предупреждение или аларма. Таймерът е конфигуриран да действа като филтър, така че кратките преходни процеси да не задействат предупреждения и аларми.
Надпис: Техники за наблюдение, базирани на състоянието
Действително наблюдаваните стойности могат да бъдат прочетени от задвижването чрез LCP, комуникация по полева шина или IoT комуникация. Освен това цифровите изходи могат да бъдат конфигурирани да реагират на специфични предупреждения и аларми. Някои устройства имат вграден уеб сървър, който може да се използва и за четене на състоянието на състоянието.
Заключение
Днес здавижванията са повече от обикновени захранващи процесори. Със способността си да действат като сензори и сензорни концентратори, да обработват, съхраняват и анализират данни, заедно с възможностите за свързване, устройствата са жизненоважни елементи в съвременните системи за автоматизация.
Задвижванията често вече присъстват в инсталациите за автоматизация и следователно представляват чудесна възможност за надграждане до Индустрия 4.0.
Това дава възможност за нови начини за извършване на поддръжка, като поддръжка, базирана на състоянието. Функциите вече са налични в някои устройства и ранните потребители вече са започнали да използват устройството като сензор.